Two-dimensional profile stretch bending chuck motion track design method for finite element simulation
A technology of motion trajectory and design method, applied in computing, special data processing applications, instruments, etc.
- Summary
- Abstract
- Description
- Claims
- Application Information
AI Technical Summary
Problems solved by technology
Method used
Image
Examples
Embodiment Construction
[0073] This embodiment is a method for designing the motion track of a two-dimensional profile stretch bending chuck for finite element simulation.
[0074] The profile bending part is a 7075-O state aluminum alloy T profile, and the length of the profile 1 is 1377mm. according to figure 1 The step-by-step design generates profile finite element simulation of the movement trajectory of the tension bending chuck. Specifically include the following steps:
[0075] Step 1: Extract and discretize the centroid guideline of the 3D digital model of the profile bending part.
[0076] Extract the centroid guide line of the 3D digital model of the curved part of the profile:
[0077] The 3D digital model of the profile bending part is obtained according to the size of the part, in CATIA from the geometric size of the part section and a guide line through sweeping, and the centroid guideline 3 of the 3D digital model of the profile bending part is extracted.
[0078] The centroid po...
PUM
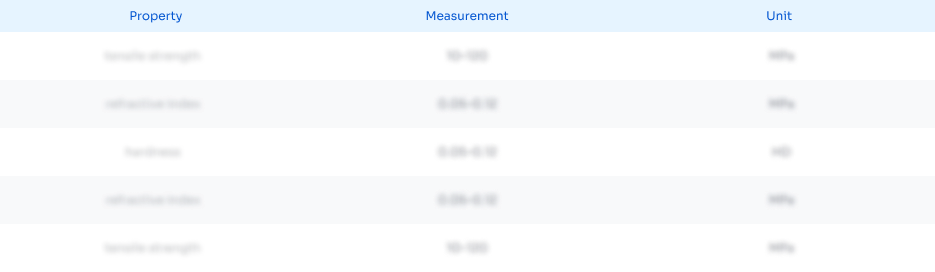
Abstract
Description
Claims
Application Information

- Generate Ideas
- Intellectual Property
- Life Sciences
- Materials
- Tech Scout
- Unparalleled Data Quality
- Higher Quality Content
- 60% Fewer Hallucinations
Browse by: Latest US Patents, China's latest patents, Technical Efficacy Thesaurus, Application Domain, Technology Topic, Popular Technical Reports.
© 2025 PatSnap. All rights reserved.Legal|Privacy policy|Modern Slavery Act Transparency Statement|Sitemap|About US| Contact US: help@patsnap.com