Compliant Constant Torque Couplings
A constant torque, coupling technology, applied in the direction of couplings, elastic couplings, mechanical equipment, etc., can solve the problems of high noise, inability to buffer vibration, low sealing precision, etc., and achieve the effect of high motion precision
- Summary
- Abstract
- Description
- Claims
- Application Information
AI Technical Summary
Problems solved by technology
Method used
Image
Examples
Embodiment Construction
[0019] The present invention will be further described in detail below in conjunction with the accompanying drawings.
[0020] A compliant constant moment coupling, including first and second half-shells 11 and 12 that are fixedly fitted, the middle part of the first half-shell 11 is fixedly connected with the driving shaft, and the middle part of the second half-shell 12 is connected to the driven shaft sleeve through a bearing The cylinder 20 constitutes a rotational fit. A compliant constant moment mechanism is arranged between the first and second half shells 11 and 12. The compliant constant moment mechanism includes a flexible connected active bracket 30 and a driven bracket 40. The active bracket 30 is fixed on the first On the half shell 11 , the driven bracket 40 is fixedly connected with the inner end of the driven shaft sleeve 20 . In the present invention, a compliant constant moment mechanism is provided in the coupling housing, and the flexible connection between...
PUM
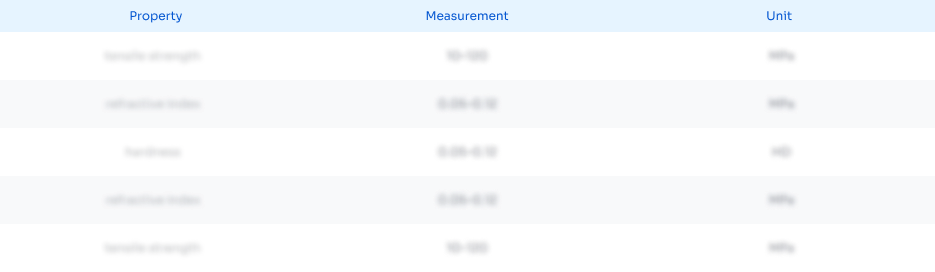
Abstract
Description
Claims
Application Information

- R&D
- Intellectual Property
- Life Sciences
- Materials
- Tech Scout
- Unparalleled Data Quality
- Higher Quality Content
- 60% Fewer Hallucinations
Browse by: Latest US Patents, China's latest patents, Technical Efficacy Thesaurus, Application Domain, Technology Topic, Popular Technical Reports.
© 2025 PatSnap. All rights reserved.Legal|Privacy policy|Modern Slavery Act Transparency Statement|Sitemap|About US| Contact US: help@patsnap.com