Gradient functional material 3D printing device and working method
A gradient functional material and 3D printing technology, applied in the field of 3D printing, can solve the problems of inability to achieve gradient printing of multi-component ceramic materials and cannot meet the requirements, and achieve the effects of high density, good surface quality and high dimensional accuracy
- Summary
- Abstract
- Description
- Claims
- Application Information
AI Technical Summary
Problems solved by technology
Method used
Image
Examples
Embodiment 2
[0052] This embodiment discloses a working method of a gradient functional material 3D printing device: image 3 shown, including the following steps:
[0053] Step 1: Fill the base paste in the raw material bin, and fill the multi-component paste with different ratios into the barrel respectively, and each barrel is filled with a multi-component paste with a corresponding ratio.
[0054] In this embodiment, the base paste is made of Al 2 o 3 Paste, multi-component paste containing 20% Si 3 N 4 Composition of Al 2 o 3 Ceramic paste, 40% Si 3 N 4 Composition of Al 2 o 3 Ceramic paste, 60% Si 3 N 4 Composition of Al 2 o 3 Ceramic paste, 80% Si 3 N 4 Composition of Al 2 o 3 Ceramic paste, the target paste is Si 3 N 4 For the paste, inject the four compatible multi-component pastes into the four barrels respectively, place the barrels on the barrel fixture, and use the upper computer to make marks in the controller.
[0055] Step 2: Input the information of t...
Embodiment 3
[0061] This embodiment discloses a working method of a gradient functional material 3D printing device, such as Figure 4 As shown, the base paste is made of ZrO 2 Paste, the target paste is stainless steel 316 paste, the multi-component paste is ZrO containing 10%, 20%, 30%, 40%, 50%, 60%, 70%, 80% stainless steel 316 2 The ceramic paste is filled in 8 barrels respectively. The part printing method is the same as that in Example 2, the difference is that the thickness of the first layer of the base paste layer is 30um, and the power of the laser is 210mW. The obtained gear structure has a smooth surface and basically no out of shape.
PUM
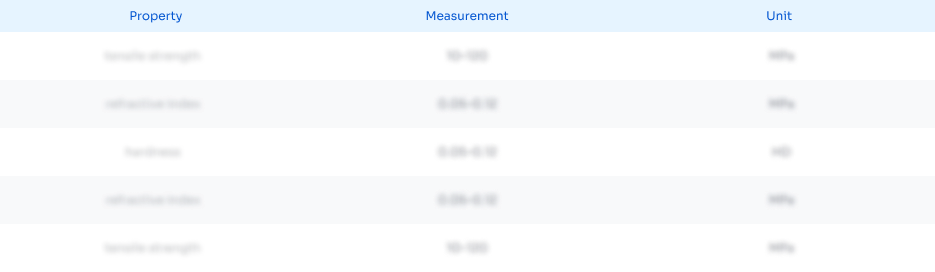
Abstract
Description
Claims
Application Information

- Generate Ideas
- Intellectual Property
- Life Sciences
- Materials
- Tech Scout
- Unparalleled Data Quality
- Higher Quality Content
- 60% Fewer Hallucinations
Browse by: Latest US Patents, China's latest patents, Technical Efficacy Thesaurus, Application Domain, Technology Topic, Popular Technical Reports.
© 2025 PatSnap. All rights reserved.Legal|Privacy policy|Modern Slavery Act Transparency Statement|Sitemap|About US| Contact US: help@patsnap.com