A maintenance method for casting molds after use
A casting mold and mold technology is applied in the maintenance field after the casting mold is used, which can solve the problems of difficulty in cleaning, uneven thickness of the oil layer, entering the cavity of the workpiece, etc., to improve the cleaning effect, and the amount is small, and the oil layer is avoided. thick effect
- Summary
- Abstract
- Description
- Claims
- Application Information
AI Technical Summary
Problems solved by technology
Method used
Image
Examples
Embodiment Construction
[0040] In order to make the technical means, creative features, goals and effects achieved by the present invention easy to understand, the present invention will be further described below in conjunction with specific illustrations. It should be noted that, in the case of no conflict, the embodiments in the present application and the features in the embodiments can be combined with each other.
[0041] like Figure 1 to Figure 9 As shown, a maintenance method for casting molds after use, the specific maintenance method steps are as follows:
[0042] S1. Mold opening: open the upper and lower molds, and take out the solidified molded parts;
[0043] S2, cooling treatment: immerse the upper and lower molds in the step S1 in a bucket filled with cold water to cool down, and the immersion time is 8-10s;
[0044] S3, drying treatment: place the cooled upper and lower molds on the drying table for natural drying;
[0045] S4. Surface cleaning of the parting surface of the upper...
PUM
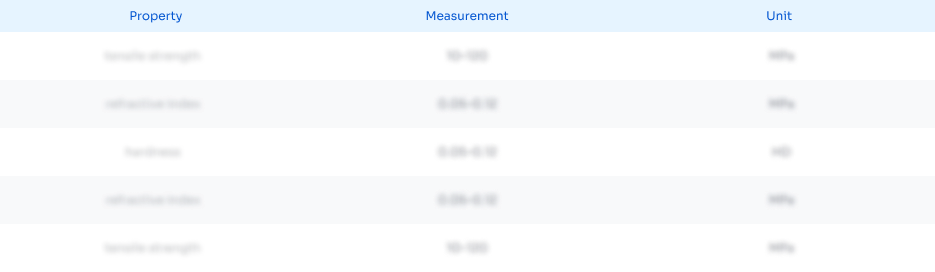
Abstract
Description
Claims
Application Information

- R&D
- Intellectual Property
- Life Sciences
- Materials
- Tech Scout
- Unparalleled Data Quality
- Higher Quality Content
- 60% Fewer Hallucinations
Browse by: Latest US Patents, China's latest patents, Technical Efficacy Thesaurus, Application Domain, Technology Topic, Popular Technical Reports.
© 2025 PatSnap. All rights reserved.Legal|Privacy policy|Modern Slavery Act Transparency Statement|Sitemap|About US| Contact US: help@patsnap.com