Displacement sensor fault-tolerant control system and method of active electromagnetic bearing
A technology of active electromagnetic bearings and displacement sensors, which is applied in the direction of electrical program control, bearings, shafts and bearings, and can solve the problems of increased size design and increased system cost
- Summary
- Abstract
- Description
- Claims
- Application Information
AI Technical Summary
Problems solved by technology
Method used
Image
Examples
Embodiment 1
[0071] The inventive idea of the present invention is: for the problems such as the increase in cost and the limited space size caused by the fault-tolerant control method of the displacement sensor 3 such as redundant sensors, the frequency spectrum mutation of the output signal of the sensor is detected by a specially designed wavelet filter, and the position of the displacement sensor 3 is judged. At the same time, the self-sensing technology of the active electromagnetic bearing 2 is used to provide the rotor displacement estimation signal after the sensor failure, so that the system can continue to operate stably according to the rotor displacement estimation signal after the sensor failure.
[0072] The displacement sensor fault-tolerant control system of the active electromagnetic bearing of the present invention includes a switching power amplifier 1, an active electromagnetic bearing 2, a displacement sensor 3, a displacement estimator 4, a fault detector 5, a switch ...
Embodiment 2
[0077] In the present invention, the active electromagnetic bearing 2 is taken as an example of a four-degree-of-freedom radial electromagnetic bearing. The present invention will be further described with specific examples below in conjunction with the accompanying drawings.
[0078] exist figure 1 In the example shown, the displacement sensor fault-tolerant control system of the active electromagnetic bearing of the present invention includes a switching power amplifier 1 , an active electromagnetic bearing 2 , a displacement sensor 3 , a displacement estimator 4 , a fault detector 5 , a switch 6 and a controller 7 .
[0079] To generate bi-directional force, the electromagnets are configured differentially. The force produced by a differentially configured electromagnet is typically linearized around a reference rotor air gap using a Taylor series:
[0080]
[0081] In the formula: μ 0 is the magnetic permeability of free space, N is the number of turns of the pole-pa...
PUM
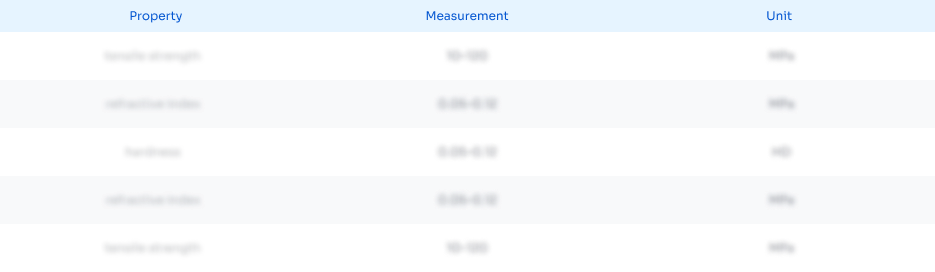
Abstract
Description
Claims
Application Information

- R&D
- Intellectual Property
- Life Sciences
- Materials
- Tech Scout
- Unparalleled Data Quality
- Higher Quality Content
- 60% Fewer Hallucinations
Browse by: Latest US Patents, China's latest patents, Technical Efficacy Thesaurus, Application Domain, Technology Topic, Popular Technical Reports.
© 2025 PatSnap. All rights reserved.Legal|Privacy policy|Modern Slavery Act Transparency Statement|Sitemap|About US| Contact US: help@patsnap.com