A modeling method for robot cables under surface constraints
A technology of surface constraints and modeling methods, which is applied in the field of robot cable modeling under surface constraints, can solve problems such as nonlinear interference, no cable method involved, and inability to model special cables to achieve a reasonable and guaranteed mechanical model. The effect of solving accuracy and ensuring global convergence
- Summary
- Abstract
- Description
- Claims
- Application Information
AI Technical Summary
Problems solved by technology
Method used
Image
Examples
Embodiment Construction
[0048] The present invention will be further described in detail below in conjunction with the accompanying drawings and embodiments.
[0049] Such as figure 1 Shown is the force analysis diagram of the high-precision manipulation robot cable.
[0050] The present invention comprises the following steps:
[0051]Step 1: Simplify the cable section of the high-precision operation robot into a circular section.
[0052] Including the following:
[0053] 1. The section of the robot cable is a rigid circular section;
[0054] 2. Neglect the shear strain of the robot cable section;
[0055] 3. The length of the robot cable is much greater than the diameter of the cable, and the diameter of the robot cable is ignored;
[0056] 4. The center line of the robot cable is a smooth curve of order 2 or higher.
[0057] Step 2: The starting point of the high-precision operation robot cable coincides with the center O of the world coordinate system. The "micro-arc section" in the high-...
PUM
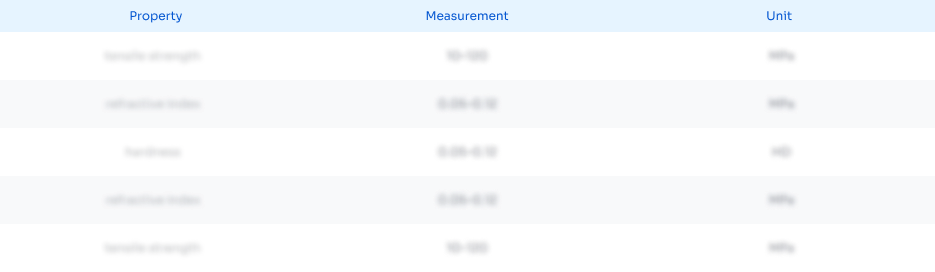
Abstract
Description
Claims
Application Information

- Generate Ideas
- Intellectual Property
- Life Sciences
- Materials
- Tech Scout
- Unparalleled Data Quality
- Higher Quality Content
- 60% Fewer Hallucinations
Browse by: Latest US Patents, China's latest patents, Technical Efficacy Thesaurus, Application Domain, Technology Topic, Popular Technical Reports.
© 2025 PatSnap. All rights reserved.Legal|Privacy policy|Modern Slavery Act Transparency Statement|Sitemap|About US| Contact US: help@patsnap.com