A Flexible Mechanism for Automatic Switching between Guide Rail Displacement Datum and Measurement Datum
A flexible mechanism and measurement reference technology, which is applied in the direction of machine gear/transmission mechanism testing, etc., can solve the problems of high guide rail positioning accuracy and achieve the effect of realizing flexible connection and reducing motion accuracy
- Summary
- Abstract
- Description
- Claims
- Application Information
AI Technical Summary
Problems solved by technology
Method used
Image
Examples
Embodiment Construction
[0012] In order to further understand the invention content, characteristics and effects of the present invention, the following examples are given, and detailed descriptions are as follows in conjunction with the accompanying drawings:
[0013] as attached figure 1 As shown, a flexible mechanism for automatic conversion of guide rail displacement reference and measurement reference is used for adaptive conversion of the high-speed end 9 of the reducer tester when it enters the measurement position with the aid of the guide rail displacement system. A measurement and positioning system based on the working installation datum of the reducer. The flexible mechanism connects the high-speed end cylinder flange of the high-speed end 9 and the guide rail moving bracket 8 of the guide rail displacement system to realize the flexible connection between the high-speed end cylinder and the guide rail displacement system; the flexible mechanism and the adapter 10 and the deceleration Th...
PUM
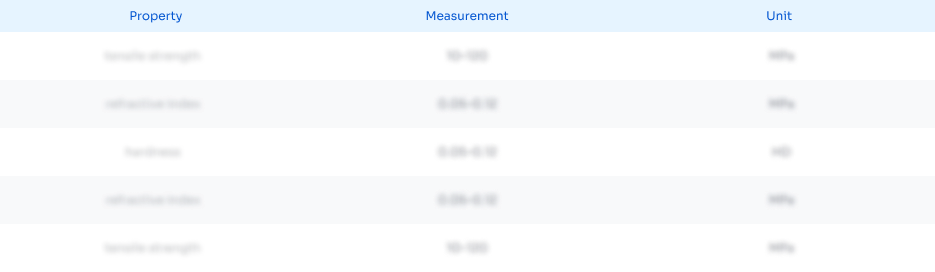
Abstract
Description
Claims
Application Information

- R&D Engineer
- R&D Manager
- IP Professional
- Industry Leading Data Capabilities
- Powerful AI technology
- Patent DNA Extraction
Browse by: Latest US Patents, China's latest patents, Technical Efficacy Thesaurus, Application Domain, Technology Topic, Popular Technical Reports.
© 2024 PatSnap. All rights reserved.Legal|Privacy policy|Modern Slavery Act Transparency Statement|Sitemap|About US| Contact US: help@patsnap.com