Piezoelectric-driven ultra-precise four-degree-of-freedom positioning and attitude adjustment mechanism and its excitation method
A piezoelectric drive, degree of freedom technology, applied in the direction of generators/motors, piezoelectric effect/electrostrictive or magnetostrictive motors, electrical components, etc., can solve complex structures and excitation methods, high prices, and limited applications range and other issues
- Summary
- Abstract
- Description
- Claims
- Application Information
AI Technical Summary
Problems solved by technology
Method used
Image
Examples
specific Embodiment 1
[0064] The following is attached with the manual figure 1 , figure 2 , image 3 , Figure 4 This embodiment will be further described in detail. This embodiment provides a figure 1 The shown ultra-precision four-degree-of-freedom positioning and attitude adjustment mechanism uses piezoelectric ceramic tubes as the main driving elements. The positioning and attitude adjustment mechanism includes a mover 1, an upper side driving foot 2, a piezoelectric ceramic tube 3, a fixed clamp block 4, a transverse guide rail 5, a longitudinal guide rail 6, a lower side driving foot 7 and a base 8; 8 stays fixed. figure 1 The axial direction of the piezoelectric ceramic tube 3 is the Z-axis direction, the horizontal direction perpendicular to the axial direction of the piezoelectric ceramic tube 3 is the Y-axis direction, and the depth direction orthogonal to the axial direction of the piezoelectric ceramic tube 3 is the X-axis The directions are represented by X-axis direction, Y-ax...
specific Embodiment 2
[0070] The following is attached with the manual figure 1 , figure 2 , image 3 , Figure 5 , Figure 6 , Figure 7 This embodiment will be further described in detail. This embodiment provides a figure 1 The excitation method of the ultra-precision four-degree-of-freedom positioning and attitude-adjusting mechanism is shown, which can realize the large-scale four-degree-of-freedom ultra-precision movement of the mover 1, including linear motion along the X-axis or Y-axis direction and around the X-axis or The rotational movement in the Y-axis direction can achieve nanoscale resolution by adjusting the amplitude and time of the excitation voltage signal. In this embodiment, the polarization direction of each partition of the piezoelectric ceramic tube 3 is as follows: figure 2 As shown, the way to apply the excitation voltage signal to the upper and lower parts of each partition electrode is as follows image 3 shown.
[0071] The excitation method for realizing the...
PUM
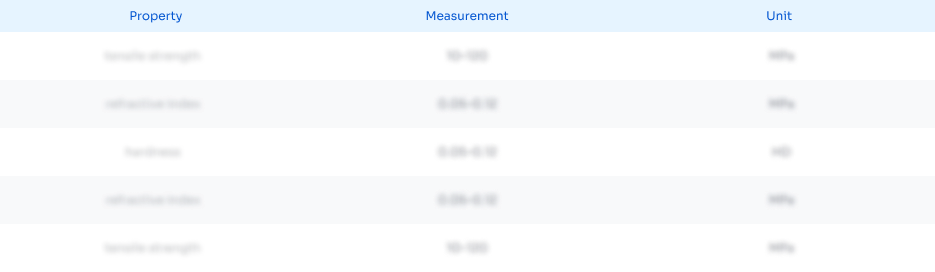
Abstract
Description
Claims
Application Information

- R&D Engineer
- R&D Manager
- IP Professional
- Industry Leading Data Capabilities
- Powerful AI technology
- Patent DNA Extraction
Browse by: Latest US Patents, China's latest patents, Technical Efficacy Thesaurus, Application Domain, Technology Topic, Popular Technical Reports.
© 2024 PatSnap. All rights reserved.Legal|Privacy policy|Modern Slavery Act Transparency Statement|Sitemap|About US| Contact US: help@patsnap.com