One-step composite twisting frame
A twisting machine and footwork technology, applied in spinning machines, continuous winding spinning machines, textiles and papermaking, etc., can solve the problems of unstable balloon tension, uneven yarn twist, blistering, etc. To achieve the effect of stable rotation speed, uniform twist and high pressure
- Summary
- Abstract
- Description
- Claims
- Application Information
AI Technical Summary
Problems solved by technology
Method used
Image
Examples
Embodiment 1
[0026] This embodiment provides a one-step compound twisting machine. By setting the unwinding device, it can effectively solve the problems of uneven twist, fuzzing, foaming, and whitening of PE threads and polyester threads when using one-step twisting machine yarns. Many points, broken ends, inconvenient operation, etc.; this composite twisting machine is suitable for 15-180 strands of PE yarn, 1000D-5000D polyester yarn, etc.
[0027] The one-step compound twisting machine can complete the single-filament twisting and compound twisting process on the same machine at one time.
[0028] Such as figure 1 and figure 2 As shown, in this example, the composite twisting machine adopts the layout of the left and right auxiliary machines and the central main machine, and two double twisting mechanisms arranged in parallel are set as the main machine, and a primary twisting mechanism is arranged on the left and right sides of the main machine as the auxiliary machine. , each auxi...
Embodiment 2
[0042] Compared with the above-mentioned embodiment 1, the difference is only in the layout of the initial twisting mechanism and the double twisting mechanism. In this example, the primary twisting mechanism is located above the double twisting mechanism, and the formed composite twister includes an upper structure, a lower structure, and a Roller drive mechanism between structures, such as Figure 6 shown.
[0043] The upper structure includes two primary twisting mechanisms arranged side by side, and the lower structure includes two double twisting mechanisms arranged side by side. The primary twisting mechanism on the left side (right side) of the upper layer structure communicates with the lower layer structure on the left side through the roller transmission mechanism. (right side) is connected to the retwisting mechanism.
PUM
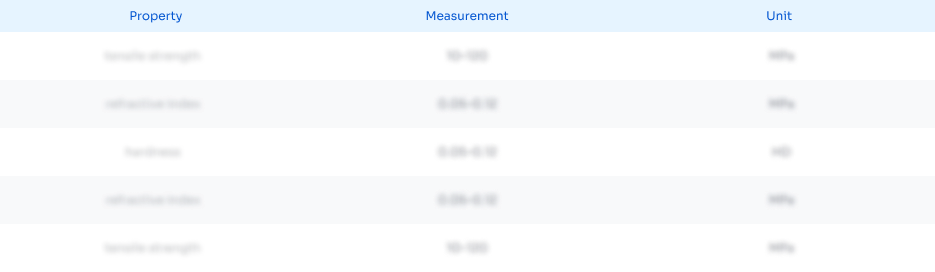
Abstract
Description
Claims
Application Information

- R&D
- Intellectual Property
- Life Sciences
- Materials
- Tech Scout
- Unparalleled Data Quality
- Higher Quality Content
- 60% Fewer Hallucinations
Browse by: Latest US Patents, China's latest patents, Technical Efficacy Thesaurus, Application Domain, Technology Topic, Popular Technical Reports.
© 2025 PatSnap. All rights reserved.Legal|Privacy policy|Modern Slavery Act Transparency Statement|Sitemap|About US| Contact US: help@patsnap.com