Linear straight-rail-type production system for textile bodies
A production system, straight-track technology, applied in textiles, papermaking, non-woven fabrics, etc., can solve the problems of low production line efficiency, restricting textile bodies, reducing material utilization, etc., to achieve good equipment connectivity and high production efficiency. Effect
- Summary
- Abstract
- Description
- Claims
- Application Information
AI Technical Summary
Problems solved by technology
Method used
Image
Examples
Embodiment 1
[0060] see figure 1 - Figure 15 , a linear straight track production system for textiles, comprising an outer sleeve 4, an air injection device 5, a linear guide rail 6, a conveying device 7, an upper mold 2 and a lower mold 3, and the upper mold 2 includes an upper mold body 21 And the upper mold cavity 22 provided inside, the lower mold 3 includes the lower mold body 31 and the lower mold cavity 32 provided inside, and the upper mold cavity 22 and the lower mold cavity 32 are butted up and down to form a molding cavity 1; The width of the inner wall of the sleeve 4 is greater than the width of the upper mold 2 and the lower mold 3, the height of the outer sleeve 4 is greater than the height of the upper mold 2, and the upper mold body 21 is provided with a plurality of upper ventilators communicating with the upper mold cavity 22. Road 25, the outer end of the upper air passage 25 communicates with the external environment of the upper mold 2, and the lower mold body 31 is...
Embodiment 2
[0062] Basic content is the same as embodiment 1, the difference is:
[0063] The air injection device 5 includes a lifting sleeve plate 57 and an air containment cover 53. The lifting cover plate 57 includes an outer plate body 571 and an inner sleeve opening 572 opened therein. The air containment cover 53 is a conical shape with a wide top and a narrow bottom. Body structure, the top of the air containment cover 53 is connected with the air outlet 51, the bottom end of the air containment cover 53 is connected with the intake pipe 56, the side wall of the air containment cover 53 is set in the inner sleeve port 572, and the outer plate body The side of 571 is connected with the output end of air cover lifting cylinder 573. The outside of the air outlet 51 is provided with an outer ring disc 52, and the top surface of the outer ring disc 52 is provided with a concentric inner air slide rail 54 and an outer air slide rail 55 around the position of the air outlet 51. Both the...
Embodiment 3
[0065] Basic content is the same as embodiment 1, the difference is:
[0066] The outer sleeve 4 includes a left half sleeve 41 and a right half sleeve 42 arranged in pairs, the left side of the left half sleeve 41 is connected with the left driving device 43, and the right side of the left half sleeve 41 part and the left side of the right half-sleeve 42 to form an outer sleeve 4, and the right side of the right half-sleeve 42 is connected to the right driving device 44; the left driving device 43 and the right driving device 44 are all higher than the lower The mold 3 is provided, and the bottom ends of the left half sleeve 41 and the right half sleeve 42 are all lower than the top surface of the lower mold body 31 but higher than the bottom surface of the lower mold body 31.
PUM
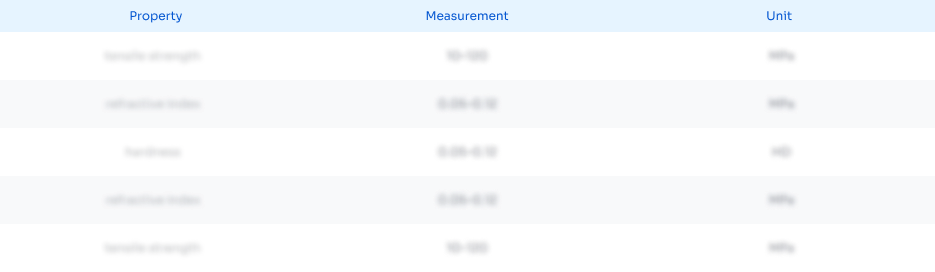
Abstract
Description
Claims
Application Information

- R&D
- Intellectual Property
- Life Sciences
- Materials
- Tech Scout
- Unparalleled Data Quality
- Higher Quality Content
- 60% Fewer Hallucinations
Browse by: Latest US Patents, China's latest patents, Technical Efficacy Thesaurus, Application Domain, Technology Topic, Popular Technical Reports.
© 2025 PatSnap. All rights reserved.Legal|Privacy policy|Modern Slavery Act Transparency Statement|Sitemap|About US| Contact US: help@patsnap.com