Preparation method of metal connection body surface spinel coating in solid oxide fuel cell
A technology of metal connectors and solid oxides, applied in fuel cells, circuits, electrical components, etc., can solve the problems of unfavorable development and application of solid oxide fuel cells, high cost, etc., and achieve low cost, controllable process, and simple equipment Effect
- Summary
- Abstract
- Description
- Claims
- Application Information
AI Technical Summary
Benefits of technology
Problems solved by technology
Method used
Image
Examples
Embodiment 1
[0043] Step 1, prepare the desired rare earth Ce doped NiMn by sol-gel method 2 o 4 Spinel powder material;
[0044] Step 2, prepare suspension, spinel powder loading is 30g L -1 , the content of nuclear power regulator is 0.8mmol·L -1 , the suspension base liquid used is acetylacetone;
[0045] Step 3, carry out surface pretreatment to Crofer 22APU ferritic stainless steel, described surface pretreatment comprises adopting 240#, 400#, 600#, 800# and 1000# SiC washing sandpaper to polish Crofer 22APU stainless steel substrate successively, Subsequent ultrasonic cleaning and drying;
[0046] Step 4, with the Crofer 22APU stainless steel substrate as the cathode, and the Pt sheet as the anode for electrophoretic deposition, the deposition time is 360s, and the deposition voltage is 100V;
[0047] Step 5, sintering the obtained composite coating using a low-temperature stepwise reduction-oxidation sintering process to obtain rare earth-doped NiMn 2 o 4 Spinel coating; the ...
Embodiment 2
[0049] Step 1, prepare the desired rare earth Ce doped NiMn by sol-gel method 2 o 4 Spinel powder material;
[0050] Step 2, prepare suspension, spinel powder loading is 30g L -1 , the content of nuclear power regulator is 1.2mmol·L -1 , the suspension base liquid used is acetylacetone;
[0051] Step 3, carry out surface pretreatment to Crofer 22APU ferritic stainless steel, described surface pretreatment comprises adopting 240#, 400#, 600#, 800# and 1000# SiC washing sandpaper to polish Crofer 22APU stainless steel substrate successively, Subsequent ultrasonic cleaning and drying;
[0052] Step 4, with the Crofer 22APU stainless steel substrate as the cathode, and the Pt sheet as the anode for electrophoretic deposition, the deposition time is 360s, and the deposition voltage is 100V;
[0053] Step 5, sintering the obtained composite coating using a low-temperature stepwise reduction-oxidation sintering process to obtain rare earth-doped NiMn 2 o 4 Spinel coating; the ...
Embodiment 3
[0055] Step 1, prepare the desired rare earth Ce doped NiMn by sol-gel method 2 o 4 Spinel powder material;
[0056] Step 2, prepare suspension, spinel powder loading is 30g L -1 , the content of nuclear power regulator is 0.8mmol·L -1 , the suspension base liquid used is acetylacetone;
[0057] Step 3, carry out surface pretreatment to Crofer 22APU ferritic stainless steel, described surface pretreatment comprises adopting 240#, 400#, 600#, 800# and 1000# SiC washing sandpaper to polish Crofer 22APU stainless steel substrate successively, Subsequent ultrasonic cleaning and drying;
[0058] Step 4, with the Crofer 22APU stainless steel substrate as the cathode, and the Pt sheet as the anode for electrophoretic deposition, the deposition time is 340s, and the deposition voltage is 100V;
[0059] Step 5, sintering the obtained composite coating using a low-temperature stepwise reduction-oxidation sintering process to obtain rare earth-doped NiMn 2 o 4 Spinel coating; the ...
PUM
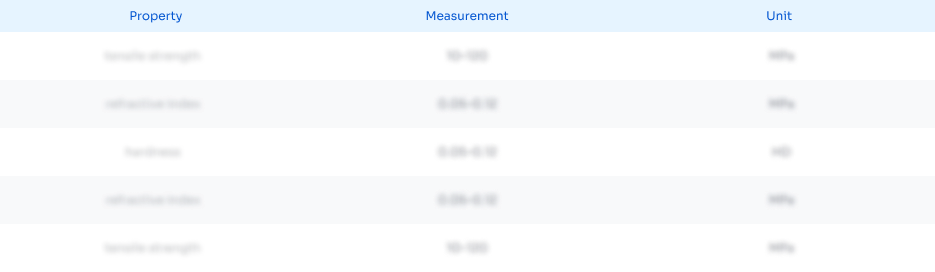
Abstract
Description
Claims
Application Information

- Generate Ideas
- Intellectual Property
- Life Sciences
- Materials
- Tech Scout
- Unparalleled Data Quality
- Higher Quality Content
- 60% Fewer Hallucinations
Browse by: Latest US Patents, China's latest patents, Technical Efficacy Thesaurus, Application Domain, Technology Topic, Popular Technical Reports.
© 2025 PatSnap. All rights reserved.Legal|Privacy policy|Modern Slavery Act Transparency Statement|Sitemap|About US| Contact US: help@patsnap.com