An Active Cam Type Lubricating Self-cleaning Mechanism
A cam-type, self-cleaning technology, applied in gear lubrication/cooling, manipulators, manufacturing tools, etc., can solve problems such as robot penetration of grease, achieve energy saving and environmental protection, reduce energy efficiency, and reduce failure probability.
- Summary
- Abstract
- Description
- Claims
- Application Information
AI Technical Summary
Problems solved by technology
Method used
Image
Examples
Embodiment Construction
[0019] The present invention will be described in further detail below in conjunction with the accompanying drawings.
[0020] Such as Figure 1~3 As shown, the present invention includes a boom 1, a small arm 7, a motor 2 and a reducer housing 3 respectively accommodated in the boom 1, a reducer input gear shaft 4, a reducer output shaft 5, an inertial double-headed piston mechanism, Oil outlet one-way valve 11, oil return one-way valve 12 and filter element 13, in which the motor 2 is statically sealed and fixedly connected to the boom 1, the output end penetrates into the boom 1, and the gear shaft 4 is input through the reducer and the output of the reducer One end of the shaft 5 is connected, one end of the reducer casing 3 is statically sealed and fixedly connected in the boom 1, and the other end is connected with the output shaft 5 of the reducer through a rotating dynamic seal 6, and the other end of the reducer casing 3 is connected to the reducer The machine input ...
PUM
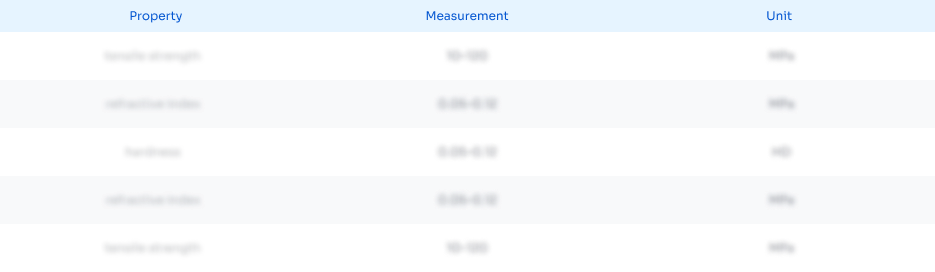
Abstract
Description
Claims
Application Information

- R&D Engineer
- R&D Manager
- IP Professional
- Industry Leading Data Capabilities
- Powerful AI technology
- Patent DNA Extraction
Browse by: Latest US Patents, China's latest patents, Technical Efficacy Thesaurus, Application Domain, Technology Topic, Popular Technical Reports.
© 2024 PatSnap. All rights reserved.Legal|Privacy policy|Modern Slavery Act Transparency Statement|Sitemap|About US| Contact US: help@patsnap.com