A method for manufacturing a carbon fiber composite multi-way joint
A technology of composite materials and multi-way joints, which is applied in the field of carbon fiber composite material multi-way joints, can solve the problems of high cost of automatic wire laying process, assembly interference of winding process parts, complex mold design of molding and RTM process, etc., to achieve The effect of satisfactory quality, low cost and simple mold structure
- Summary
- Abstract
- Description
- Claims
- Application Information
AI Technical Summary
Problems solved by technology
Method used
Image
Examples
specific Embodiment approach 1
[0031] The manufacturing method of the carbon fiber composite multi-way joint of the present embodiment is realized according to the following steps:
[0032] Step 1: Mold treatment: Remove oil stains, water stains and dust on the 3 / 4 petal structure and 1 / 4 petal structure molds of the formed carbon fiber composite multi-way joint, and evenly coat the outer surface of the mold with carbon fiber composite materials. Mold agent 3 times, each interval 15min;
[0033] Step 2: Forming the two-petal structure: Lay the prepreg fabric that has been cut according to the design, and manually lay it on the mold with the two-petal structure. The laying method is that after the first layer is laid, under a negative atmospheric pressure, Pre-compact for 15 minutes, and then pre-compact once every 4 layers until the laying is completed. The fabric is 6k carbon fiber fabric;
[0034] Step 3: Curing in the curing oven: Lay the release cloth, isolation film, air felt and vacuum bag from the i...
specific Embodiment approach 2
[0042] The manufacturing method of the carbon fiber composite multi-way joint of the present embodiment is realized according to the following steps:
[0043] Step 1. Mold treatment: Remove oil stains, water stains and dust on the 3 / 4 petal structure and 1 / 4 petal structure molds of the formed carbon fiber composite multi-way joint, and evenly coat the outer surface of the mold with carbon fiber composite materials. Molding agent 2 times, each interval 10min;
[0044] Step 2. Forming of the two-petal structure: Lay the prepreg that has been cut according to the design, and manually lay it on the mold with the two-petal structure. Compact for 10 minutes, and then pre-compact once every 5 layers until the laying is completed, and the fabric is 3k carbon fiber fabric;
[0045] Step 3. Autoclave curing: Lay the release cloth, isolation film, air felt and vacuum bag sequentially from the inside to the outside. After the vacuum bag is pressed, the autoclave is cured. According to t...
specific Embodiment approach 3
[0053] The manufacturing method of the carbon fiber composite multi-way joint of the present embodiment is realized according to the following steps:
[0054] Step 1. Mold treatment: Remove oil stains, water stains and dust on the 3 / 4 petal structure and 1 / 4 petal structure molds of the formed carbon fiber composite multi-way joint, and evenly coat the outer surface of the mold with carbon fiber composite materials. Mold agent 3 times, each interval 10min;
[0055] Step 2. Forming of the two-petal structure: Lay the cut fabric according to the design, and manually lay it on the mold of the two-petal structure. The laying method is that after the first layer is laid, it is pre-compacted under a negative atmospheric pressure. 20min, then pre-compact every 4 layers until the laying is completed, the fabric is 12k carbon fiber fabric;
[0056] Step 3. Curing in the curing oven: Lay out the mold release cloth, guide net, winding pipe and vacuum bag in sequence from the inside to t...
PUM
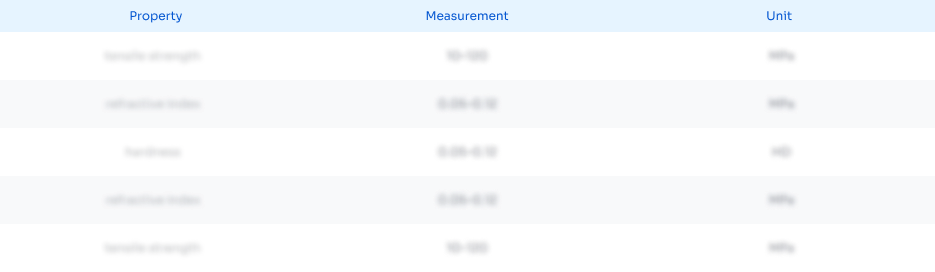
Abstract
Description
Claims
Application Information

- R&D Engineer
- R&D Manager
- IP Professional
- Industry Leading Data Capabilities
- Powerful AI technology
- Patent DNA Extraction
Browse by: Latest US Patents, China's latest patents, Technical Efficacy Thesaurus, Application Domain, Technology Topic, Popular Technical Reports.
© 2024 PatSnap. All rights reserved.Legal|Privacy policy|Modern Slavery Act Transparency Statement|Sitemap|About US| Contact US: help@patsnap.com