High concentration SO2 conversion acid making technology
A SO2, high-concentration technology, applied in the direction of inorganic chemistry, sulfur compounds, chemical instruments and methods, etc., can solve the problems of acid conversion, large size of dry suction equipment, limitation of comprehensive economic benefits of oxygen-enriched smelting, etc., and achieve low complexity , The effect of simple process
- Summary
- Abstract
- Description
- Claims
- Application Information
AI Technical Summary
Problems solved by technology
Method used
Image
Examples
Embodiment 1
[0030] combined with figure 1 The present invention is described in detail as follows with embodiment:
[0031] SO in wet flue gas from purification process 2 The concentration is 29%, O 2 The concentration is 10%, first enter the drying tower for dehydration (no air leakage), then enter the pre-II heat exchanger, the gas temperature rises from 45°C to 190°C, then enter the pre-I heat exchanger, the temperature rises to 390°C, and then enter the pre-heat exchanger A layer of catalyst in the converter reacts, and SO in the flue gas after the reaction 2 concentration down to 22%, O 2 concentration down to 6.5%, SO 3 The concentration is 7%. The 600°C high-temperature flue gas from the pre-first layer conversion reaction first passes through the pre-I heat exchanger and cools down to 400°C, and then enters the pre-two-layer catalyst for conversion. After the reaction, SO in the flue gas 2 concentration down to 15%, O 2 concentration down to 3%, SO 3 The concentration is 14...
Embodiment 2
[0034] combined with figure 2 The present invention is described in detail as follows with embodiment:
[0035] SO in wet flue gas from purification process 2 The concentration is 18%, O 2 The concentration is 17%, first enters the drying tower for dehydration (no air leakage), and then enters the pre-I heat exchanger; the gas temperature rises from 45°C to 420°C, and then enters the pre-reformer for a layer of catalyst reaction. After the reaction, SO in the flue gas 2 concentration down to 11%, O 2 concentration down to 13.5%, SO 3The concentration is 7%, and the 600°C high-temperature flue gas from the conversion reaction of the first layer passes through the pre-I heat exchanger and cools down to 255°C, and then enters the economizer to preheat the boiler feed water; the flue gas temperature drops to 190°C and then enters The pre-absorption tower conducts the first absorption to make acid; absorbs SO 3 SO in flue gas after 60℃ 2 concentration rose to 11.8%, O 2 The...
Embodiment 3
[0038] combined with image 3 The present invention is described in detail as follows with embodiment:
[0039] Contains SO from the purification process 2 The wet flue gas with a concentration of more than 40% first enters the drying tower for dehydration, and the drying tower distributes air to the SO in the flue gas 2 Concentration 37%, O 2 After the concentration is 13%, it enters the pre-II heat exchanger; after the pre-II heat exchange, the gas temperature rises from 45°C to 190°C, then enters the pre-I heat exchanger, and the temperature rises to 400°C, and then enters the pre-reformer with a layer of catalyst reaction, SO in the flue gas after the reaction 2 concentration down to 30%, O 2 concentration down to 9.5%, SO 3 The concentration is 7%. The 600°C high-temperature flue gas from the pre-first layer conversion reaction first passes through the pre-I heat exchanger and cools down to 400°C, and then enters the pre-two-layer catalyst for conversion. After the r...
PUM
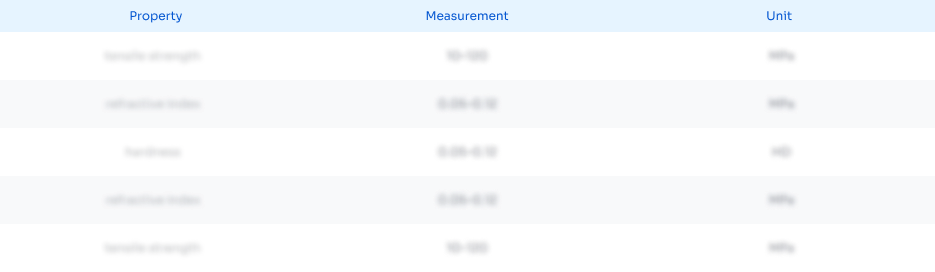
Abstract
Description
Claims
Application Information

- Generate Ideas
- Intellectual Property
- Life Sciences
- Materials
- Tech Scout
- Unparalleled Data Quality
- Higher Quality Content
- 60% Fewer Hallucinations
Browse by: Latest US Patents, China's latest patents, Technical Efficacy Thesaurus, Application Domain, Technology Topic, Popular Technical Reports.
© 2025 PatSnap. All rights reserved.Legal|Privacy policy|Modern Slavery Act Transparency Statement|Sitemap|About US| Contact US: help@patsnap.com