Active vibration inhibition execution mechanism of flexible structure
A flexible structure and actuator technology, applied in the directions of space navigation equipment, tools, transportation and packaging, can solve the problems of large space size, complex structure, unsuitable for distributed active vibration control, etc., achieve small space size, enlarged output The effect of thrust, reduced output requirements
- Summary
- Abstract
- Description
- Claims
- Application Information
AI Technical Summary
Problems solved by technology
Method used
Image
Examples
Embodiment Construction
[0027] The specific implementation and functional principles of the present invention will be further described in detail below in conjunction with the accompanying drawings.
[0028] like figure 1 As shown, the actuator is composed of an upper platform, a lower platform, a linear drive, a universal joint, a wedge-shaped slider, a reversing support block, and supporting guide rails. Using the transmission principle of a wedge-shaped mechanism, the wedge-shaped slider The linear motion in the x direction is converted into the linear motion of the reversing support block in the z direction perpendicular to the platform plane, so as to realize the two-degree-of-freedom relative rotation between the upper and lower platforms and the control torque output.
[0029] in:
[0030] platform ( figure 1 middle number 1), lower platform ( figure 1 Middle number 2) is respectively connected with the two substructures of the flexible structure, and the upper and lower platforms are conne...
PUM
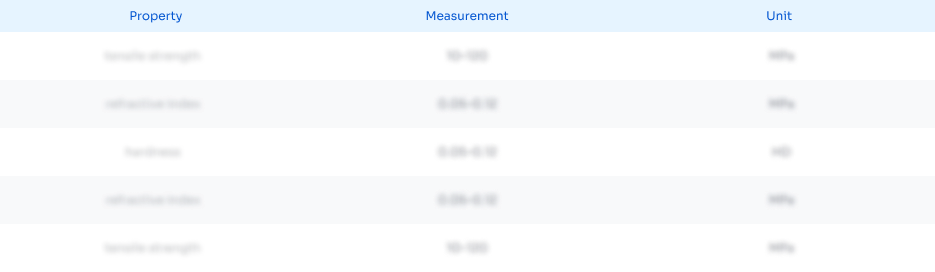
Abstract
Description
Claims
Application Information

- Generate Ideas
- Intellectual Property
- Life Sciences
- Materials
- Tech Scout
- Unparalleled Data Quality
- Higher Quality Content
- 60% Fewer Hallucinations
Browse by: Latest US Patents, China's latest patents, Technical Efficacy Thesaurus, Application Domain, Technology Topic, Popular Technical Reports.
© 2025 PatSnap. All rights reserved.Legal|Privacy policy|Modern Slavery Act Transparency Statement|Sitemap|About US| Contact US: help@patsnap.com