Device and method for actively inhibiting rollback movement of parasitic motion principle piezoelectric actuator
A technology of piezoelectric drive and parasitic motion, applied in the direction of piezoelectric effect/electrostrictive or magnetostrictive motors, electrical components, generators/motors, etc., which can solve the problems of overturning moment, driving efficiency and positioning accuracy limitations , large additional friction and other issues, to achieve the effect of ensuring linear output characteristics, improving driving performance, and improving motion characteristics
- Summary
- Abstract
- Description
- Claims
- Application Information
AI Technical Summary
Problems solved by technology
Method used
Image
Examples
Embodiment
[0039] see figure 2 , Figure 4 As shown, when an electrical signal with a certain amplitude and frequency is applied to the driving piezoelectric stack 7 alone, the driving piezoelectric stack 7 will elongate S due to its inverse piezoelectric effect. 1 , so that the driving lever rotates around point C, and the displacement S generated by driving the piezoelectric stack 7 1 Zoom in, and apply a frictional force f to slider 6 N1 with positive pressure N 1 , and then make it move Δy along the negative direction of y. Due to the existence of parasitic motion along the negative x direction at point A of the driving lever, the positive pressure N of point A on the slider 6 is 1 Increases as the drive lever is turned.
[0040] see image 3 , Figure 4 As shown, when an electrical signal with a certain amplitude and frequency is applied to the lifting piezoelectric stack 3 alone, the driving piezoelectric stack 3 will elongate S due to its inverse piezoelectric effect 2 , ...
PUM
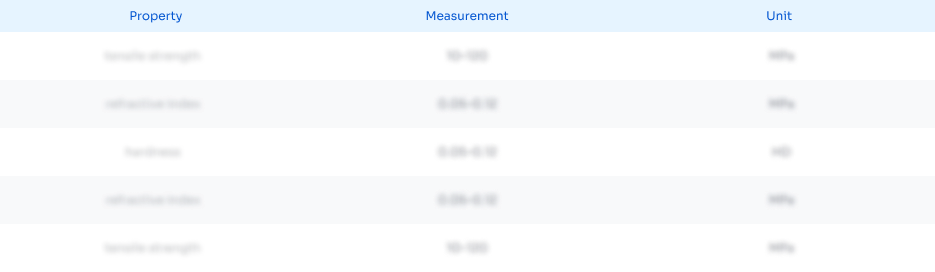
Abstract
Description
Claims
Application Information

- R&D
- Intellectual Property
- Life Sciences
- Materials
- Tech Scout
- Unparalleled Data Quality
- Higher Quality Content
- 60% Fewer Hallucinations
Browse by: Latest US Patents, China's latest patents, Technical Efficacy Thesaurus, Application Domain, Technology Topic, Popular Technical Reports.
© 2025 PatSnap. All rights reserved.Legal|Privacy policy|Modern Slavery Act Transparency Statement|Sitemap|About US| Contact US: help@patsnap.com