A two-state variable stiffness compliant joint and its operating method
A variable stiffness, two-state technology, applied in the field of robotics, can solve problems such as difficulty in ensuring joint stiffness, and achieve the effects of good human-computer interaction safety, good impact resistance, and good torque transmission characteristics.
- Summary
- Abstract
- Description
- Claims
- Application Information
AI Technical Summary
Problems solved by technology
Method used
Image
Examples
Embodiment 1
[0036] like figure 1 and figure 2 As shown, a two-state variable stiffness compliant joint at least includes an input shaft 1, an output outer ring 2 and a stiffness adjustment mechanism: the input shaft 1 is set at the center of rotation of the output outer ring 2, and is the same as the input shaft 1 The input disk 4 of the shaft center is fixedly connected, and the output outer ring 2 is connected with the input disk 4 through a rotating pair; the input disk 4 and the output outer ring 2 are connected through a supporting elastic reed 5; the stiffness adjustment mechanism includes a stiffness adjustment motor 8, a second Two bevel gears 9, the first bevel gear 3; the motor 8 is fixedly connected with a second bevel gear 9; the second bevel gear 9 meshes with two first bevel gears 3 that are fixedly connected with the elastic reed 5 to form a gear transmission connection .
[0037] There are multiple (3-6) elastic reeds 5, the plurality of elastic reeds 5 are evenly distr...
Embodiment 2
[0041] like image 3 As shown, the main frame of this example is a frame 10, on which a motor bracket 11 is installed; the main motor 12 is fixed on the motor bracket 11 through a flange, and is connected to the input shaft 1 through a conveyor belt 15, and the harmonic reducer 13 to the transmission mechanism, the transmission shaft is connected with the input disk 4, connected with the power output outer ring 2 through the elastic reed 5, and the elastic reed 5 is connected with the input disk 4 and the output outer ring 2 by the bearing 6.
[0042] The adjusting motor 8 is fixed on the input disc 4 through a flange, and is connected with the second bevel gear 9 through the adjusting motor coupling, and the first bevel gear 3 is fixedly connected with the elastic reed 5 .
[0043] When this example is running, the input disk 4 is rigidly driven by the main motor 12, and the elastic reed 5 is deformed to drive the output outer ring 2 to rotate. When the stiffness adjustment m...
PUM
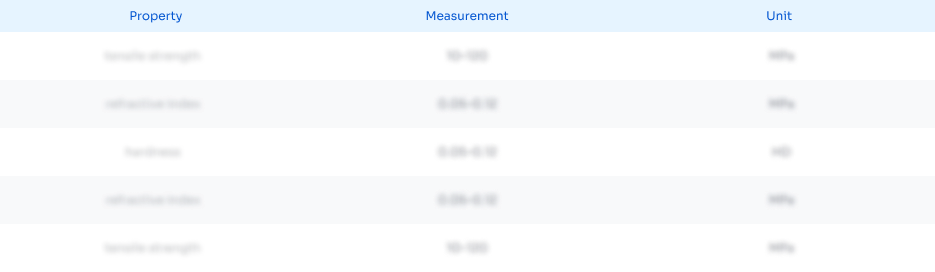
Abstract
Description
Claims
Application Information

- Generate Ideas
- Intellectual Property
- Life Sciences
- Materials
- Tech Scout
- Unparalleled Data Quality
- Higher Quality Content
- 60% Fewer Hallucinations
Browse by: Latest US Patents, China's latest patents, Technical Efficacy Thesaurus, Application Domain, Technology Topic, Popular Technical Reports.
© 2025 PatSnap. All rights reserved.Legal|Privacy policy|Modern Slavery Act Transparency Statement|Sitemap|About US| Contact US: help@patsnap.com