Piezoelectric-driven passive pliant microclamp
A piezoelectric drive, micro-clamp technology, applied in the field of micro-clamp, can solve the problems of low positioning accuracy of the clamped object, small stroke range of the micro-clamp, uneven force state, etc., to achieve uniform force state and increase the stroke range. , the effect of reducing the size of the structure
- Summary
- Abstract
- Description
- Claims
- Application Information
AI Technical Summary
Problems solved by technology
Method used
Image
Examples
specific Embodiment approach 1
[0018] Specific implementation mode one: as figure 1 and figure 2 As shown, the piezoelectric driven passive compliant micro gripper of this embodiment includes a base 1, a bridge-type amplifying mechanism 2, a piezoelectric ceramic 3, two lever arms 4, two connecting hinges 5, and two clamping arms 6. Two force-measuring strain gauges 7 and two jaws 8. The bridge-type amplifying mechanism 2 is a four-frame structure. The upper and lower ends of the bridge-type amplifying mechanism 2 are the displacement input ends of the bridge-type amplifying mechanism 2. The bridge-type amplifying mechanism The middle part of both sides of 2 is the displacement output end of the bridge type amplifying mechanism 2, the displacement output part of each side of the bridge type amplifying mechanism 2 is a double-layer structure, the piezoelectric ceramic 3 is vertically arranged inside the bridge type amplifying mechanism 2 and the piezoelectric ceramic The two ends of 3 are in contact with t...
specific Embodiment approach 2
[0019] Specific implementation mode two: as figure 1 and figure 2 As shown, the clamping arm 6 in this embodiment has a parallelogram structure, and a load-measuring strain gauge 7 is provided on the inner wall of the parallelogram structure of each clamping arm 6 . In such a design, the piezoelectric-driven passively compliant micro-clamp of the present invention introduces the design concept of passive compliant, and designs the stiffness of the parallelogram clamping arm, so that the position control of the micro-clamp system does not need to rely on the position sensor, and only needs to be opened. Ring control is sufficient, thereby simplifying the system structure. Other components and connections are the same as those in the first embodiment.
[0020] Clamping arm 6 stiffness design principles:
[0021] The stiffness of the clamping arm 6 is less than or equal to the ratio of the maximum error of the open-loop position control to the maximum bearing force of the obj...
specific Embodiment approach 3
[0025] Specific implementation mode three: as figure 1 and figure 2 As shown, the connection hinge 5 in this embodiment is a sheet-shaped connection hinge. With such a design, the lever arm 4 can be enlarged twice through the leaf hinge 5 to achieve a magnification of 50 times, ensuring the stability of the magnification of the lever arm 4 . Other compositions and connections are the same as those in Embodiment 1 or 2.
PUM
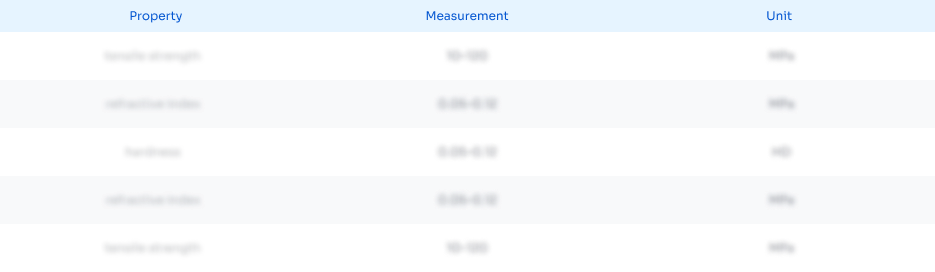
Abstract
Description
Claims
Application Information

- R&D
- Intellectual Property
- Life Sciences
- Materials
- Tech Scout
- Unparalleled Data Quality
- Higher Quality Content
- 60% Fewer Hallucinations
Browse by: Latest US Patents, China's latest patents, Technical Efficacy Thesaurus, Application Domain, Technology Topic, Popular Technical Reports.
© 2025 PatSnap. All rights reserved.Legal|Privacy policy|Modern Slavery Act Transparency Statement|Sitemap|About US| Contact US: help@patsnap.com