Continuous casting machine before-cutting roller way cooling system
A technology of cooling system and front roller table, which is applied in the field of continuous casting machine equipment, can solve the problems of low maintenance operation efficiency, increased production cost, production stagnation, etc., and achieve the effect of improving maintenance efficiency, increasing service life, and reducing the number of opening and closing
- Summary
- Abstract
- Description
- Claims
- Application Information
AI Technical Summary
Problems solved by technology
Method used
Image
Examples
Embodiment Construction
[0010] Below, the present invention will be described in further detail in conjunction with the accompanying drawings.
[0011] Such as figure 1 As shown, a cooling system for the front-cutting roller table of a continuous casting machine is used to provide circulating cooling water to each roller 20 of the front-cutting roller table, and the said front-cutting roller table has a plurality of streams 30 arranged in parallel, Each of said streams 30 has the same number of said rollers 20 . The mode of this embodiment takes the actual production situation of a continuous casting workshop of a steelmaking plant as an example. The roller table before cutting has seven streams, and each stream has 15 rollers.
[0012] The cooling system includes water inlet main pipe 1, water inlet main valve 2 installed on water inlet main pipe 1, return water main pipe 3, return water main valve 4 installed on return water main pipe 3, water inlet main pipe 1 and return water main pipe 3 are ma...
PUM
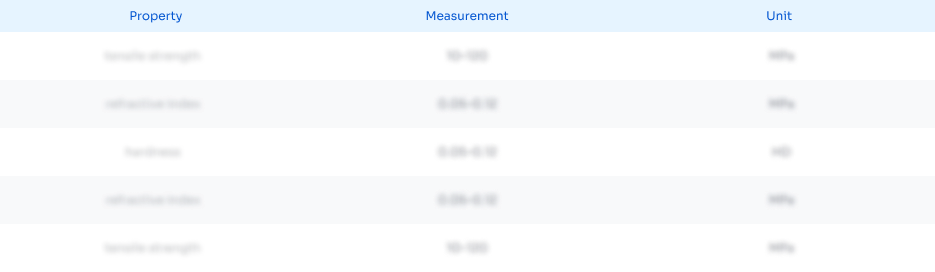
Abstract
Description
Claims
Application Information

- Generate Ideas
- Intellectual Property
- Life Sciences
- Materials
- Tech Scout
- Unparalleled Data Quality
- Higher Quality Content
- 60% Fewer Hallucinations
Browse by: Latest US Patents, China's latest patents, Technical Efficacy Thesaurus, Application Domain, Technology Topic, Popular Technical Reports.
© 2025 PatSnap. All rights reserved.Legal|Privacy policy|Modern Slavery Act Transparency Statement|Sitemap|About US| Contact US: help@patsnap.com