Injection tool and method to seal insert parts
A technology of inserting parts, injection molding and encapsulation, applied in the direction of coating, etc., can solve the problems of inability to completely seal and withstand high temperature, and achieve the effect of good sealing
- Summary
- Abstract
- Description
- Claims
- Application Information
AI Technical Summary
Problems solved by technology
Method used
Image
Examples
Embodiment Construction
[0021] For the injection molding of inserts, thermosetting plastics are usually used as flowable materials, since they become very low-viscosity during the injection molding process and can therefore be used very well to fill thin-walled areas. However, it also tends to flow into areas that should not be overmolded, that is, where there should be no thermoset after injection molding is complete. These are, for example, electrical or electronic components, over which the thermosetting plastic flows during injection molding, since they are not completely sealed by the contact surfaces. This occurs because, due to manufacturing tolerances, there may be unevennesses in the insert, which cannot be completely sealed by the metal contact surfaces used hitherto. Flow into undesired areas necessitates costly reprocessing. This is especially a problem when injecting electrical or electronic components, since as little mechanical stress as possible is applied to these components in orde...
PUM
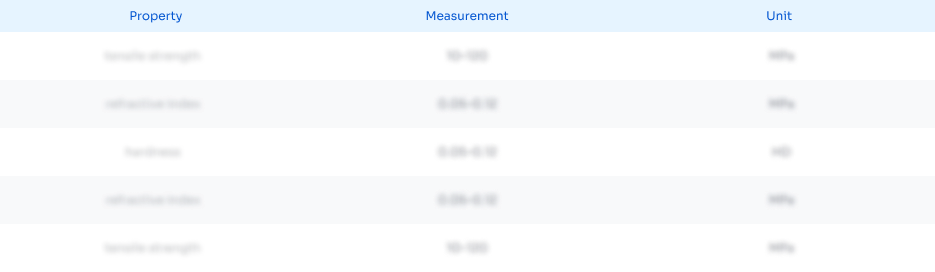
Abstract
Description
Claims
Application Information

- R&D Engineer
- R&D Manager
- IP Professional
- Industry Leading Data Capabilities
- Powerful AI technology
- Patent DNA Extraction
Browse by: Latest US Patents, China's latest patents, Technical Efficacy Thesaurus, Application Domain, Technology Topic, Popular Technical Reports.
© 2024 PatSnap. All rights reserved.Legal|Privacy policy|Modern Slavery Act Transparency Statement|Sitemap|About US| Contact US: help@patsnap.com