Movement support arm moment balancing device
A technology of balance device and arm strength, applied in the field of torque control, which can solve problems such as unstable load, increased system weight, and large motor torque, and achieve the effects of preventing deformation in other directions, high environmental adaptability, and easy replacement
- Summary
- Abstract
- Description
- Claims
- Application Information
AI Technical Summary
Problems solved by technology
Method used
Image
Examples
Embodiment Construction
[0018] The following will clearly and completely describe the technical solutions in the embodiments of the present invention with reference to the drawings in the embodiments of the present invention. Based on the embodiments of the present invention, all other embodiments obtained by persons of ordinary skill in the art without making creative efforts belong to the protection scope of the present invention.
[0019] Such as figure 1 , 2 , 3, 4 and 5, the shell of the present invention and the output flange 1 and the input flange 10 arranged on the shell; the shell is formed by covering the side cover plate 2 and the shell bottom 3 with a concave cavity; A transmission mechanism is also provided in the cavity, the transmission mechanism includes a planet carrier 4, a spring 5, a spring guide groove 6, a planetary gear 7, a sun gear 8, an external gear 9 and a bearing 11, and the input flange 10 is fixed At one end of the inner ring of the bearing 11, the sun gear 8 is fixe...
PUM
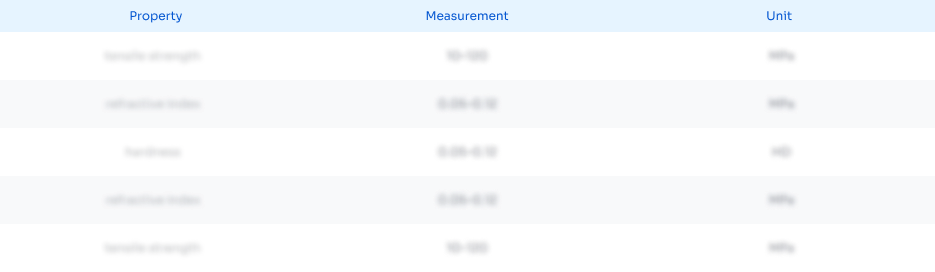
Abstract
Description
Claims
Application Information

- R&D Engineer
- R&D Manager
- IP Professional
- Industry Leading Data Capabilities
- Powerful AI technology
- Patent DNA Extraction
Browse by: Latest US Patents, China's latest patents, Technical Efficacy Thesaurus, Application Domain, Technology Topic, Popular Technical Reports.
© 2024 PatSnap. All rights reserved.Legal|Privacy policy|Modern Slavery Act Transparency Statement|Sitemap|About US| Contact US: help@patsnap.com