Semi-dry method-wet method series SO2 flue gas desulfurization process and device
A semi-dry desulfurization and desulfurization process technology, which is applied in the field of flue gas treatment equipment, can solve the problems of high desulfurization efficiency and high energy consumption in operation, and achieve the effect of increasing oxidation rate, high desulfurization efficiency, and no waste water discharge
- Summary
- Abstract
- Description
- Claims
- Application Information
AI Technical Summary
Problems solved by technology
Method used
Image
Examples
Embodiment 1
[0045] Process A: The first-stage desulfurization adopts rotary spray desulfurization, and the second-stage desulfurization adopts wet desulfurization. The schematic diagram of the two-stage serial desulfurization process is as follows figure 1 shown.
[0046] The desulfurization device includes an electrostatic precipitator 2 , a rotary atomization desulfurization tower 7 , a bag filter 11 , a booster induced draft fan 15 and a spray desulfurization tower 24 arranged in sequence along the flow direction of the flue gas.
[0047] The bottom of the electrostatic precipitator is connected to the dust bin 3, and the rotary atomization desulfurization tower 7 is a conventional rotary spray desulfurization tower, including the tower body and the rotary sprayer 6 installed in the tower body. The desulfurizer supply device includes a desulfurizer bin A8, a slurry tank A9 and a slurry supply pump A10 arranged in sequence, and the slurry supply pump A is connected to the high-level liq...
Embodiment 2
[0058] Process B: The first stage desulfurization adopts circulating fluidized bed desulfurization, and the second stage desulfurization adopts wet desulfurization. The schematic diagram of the two-stage serial desulfurization process is as follows figure 2 shown.
[0059] Except for the semi-dry desulfurization tower, the device part is the same as that of the embodiment A.
[0060] In this embodiment, the semi-dry desulfurization tower adopts a circulating fluidized bed 32 with a circulating fluidized bed tower inlet 33 and a desulfurization ash return tower inlet 34, and the circulating fluidized bed tower inlet 33 is connected to the outlet of the electrostatic precipitator , the desulfurization ash return tower inlet 34 is connected to the desulfurization ash outlet of the bag filter 11 , the desulfurization agent bin A8 is connected to the high-level storage bin 31 , and the high-level storage bin 31 is connected to the circulating fluidized bed 32 .
[0061] high conc...
PUM
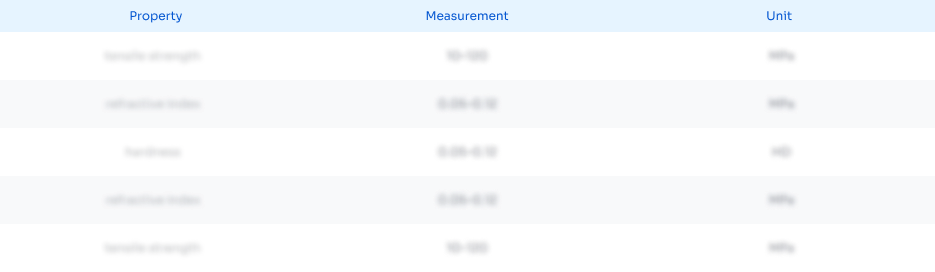
Abstract
Description
Claims
Application Information

- Generate Ideas
- Intellectual Property
- Life Sciences
- Materials
- Tech Scout
- Unparalleled Data Quality
- Higher Quality Content
- 60% Fewer Hallucinations
Browse by: Latest US Patents, China's latest patents, Technical Efficacy Thesaurus, Application Domain, Technology Topic, Popular Technical Reports.
© 2025 PatSnap. All rights reserved.Legal|Privacy policy|Modern Slavery Act Transparency Statement|Sitemap|About US| Contact US: help@patsnap.com