High-precision shadow-mask-deposition system and method therefor
A mask and shadow-shading technology, which is applied in the field of thin film deposition based on evaporation, can solve the problems of reducing display brightness and unsatisfactory, and achieve the effect of reducing feathering
- Summary
- Abstract
- Description
- Claims
- Application Information
AI Technical Summary
Problems solved by technology
Method used
Image
Examples
Embodiment Construction
[0027] Figure 1 depicts a schematic diagram of a cross-section of the main features of a direct patterned deposition system according to the prior art. System 100 is a conventional evaporation system that deposits a desired pattern of material on a substrate by evaporating material through a shadow mask positioned in front of the substrate. System 100 includes a source 104 and a shadow mask 106 arranged within a low pressure vacuum chamber (not shown).
[0028] Substrate 102 is a glass substrate suitable for forming an active matrix organic light emitting diode (AMOLED) display. Substrate 102 includes surface 114 defining plane 108 and vertical axis 110 . Vertical axis 110 is normal to plane 108 . Surface 114 includes a plurality of deposition sites G for receiving green light emitting material, a plurality of deposition sites B for receiving blue light emitting material, and a plurality of deposition sites R for receiving red light emitting material. The deposition sites a...
PUM
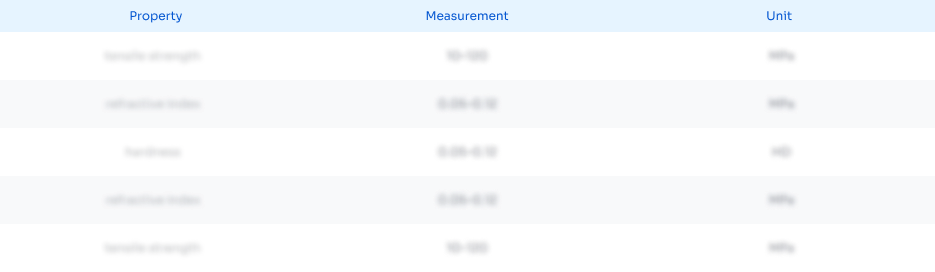
Abstract
Description
Claims
Application Information

- R&D
- Intellectual Property
- Life Sciences
- Materials
- Tech Scout
- Unparalleled Data Quality
- Higher Quality Content
- 60% Fewer Hallucinations
Browse by: Latest US Patents, China's latest patents, Technical Efficacy Thesaurus, Application Domain, Technology Topic, Popular Technical Reports.
© 2025 PatSnap. All rights reserved.Legal|Privacy policy|Modern Slavery Act Transparency Statement|Sitemap|About US| Contact US: help@patsnap.com