Method for determining sheet stamping springback compensation factor
A technology of springback compensation and thin plate stamping, which is applied in the field of thin plate stamping springback, can solve the problems that the simulation results are not completely reliable and the prediction accuracy is not very high, and achieve the effect of reliable springback data and improved accuracy
- Summary
- Abstract
- Description
- Claims
- Application Information
AI Technical Summary
Problems solved by technology
Method used
Image
Examples
specific Embodiment approach 1
[0032] Specific implementation mode 1: A method for determining the springback compensation factor of thin plate stamping in this embodiment, the method for determining the springback compensation factor of thin plate stamping can be realized by the following steps:
[0033] Step 1: According to the geometric dimensions of the designed mold, reverse solve the standard stamping parts, that is, the geometric dimensions of the ideal parts without springback;
[0034] Step 2: According to the geometric dimensions of the standard stamping parts obtained by the reverse solution, in the computer, use 3D drawing software to establish the model of the standard stamping parts;
[0035] Step 3: Import the model of the established standard stamping part into the finite element numerical simulation software for mesh division to obtain a meshed finite element model;
[0036] Step 4: Record the spatial position of each node in the finite element model of the obtained standard stamping parts,...
specific Embodiment approach 2
[0055] Specific embodiment 2: Different from specific embodiment 1, in the method for determining the springback compensation factor of thin plate stamping in this embodiment, the calculation of the offset distance of each corresponding node as described in step 6 and step 11 requires the use of finite elements Utilities tools for numerical simulation software.
specific Embodiment approach 3
[0056] Embodiment 3: Different from Embodiment 1, in this embodiment, a method for determining the springback compensation factor of thin plate stamping uses the same type and specification of blanks and the same set of molds for the three trial stampings described in step 8.
PUM
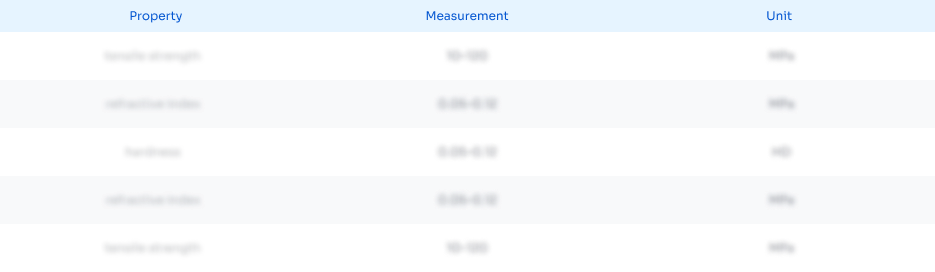
Abstract
Description
Claims
Application Information

- Generate Ideas
- Intellectual Property
- Life Sciences
- Materials
- Tech Scout
- Unparalleled Data Quality
- Higher Quality Content
- 60% Fewer Hallucinations
Browse by: Latest US Patents, China's latest patents, Technical Efficacy Thesaurus, Application Domain, Technology Topic, Popular Technical Reports.
© 2025 PatSnap. All rights reserved.Legal|Privacy policy|Modern Slavery Act Transparency Statement|Sitemap|About US| Contact US: help@patsnap.com