Bridge crane and control method
A bridge crane and bridge frame technology, which is applied in the field of bridge crane and control, can solve problems such as cable wear, hidden safety hazards, winding, etc., and achieve the effect of reducing wear and improving safety
- Summary
- Abstract
- Description
- Claims
- Application Information
AI Technical Summary
Problems solved by technology
Method used
Image
Examples
Embodiment 2
[0051] Embodiment 2: a control method of a bridge crane, comprising the following steps:
[0052] S1: According to the grabbing parameters of the electric grab bucket, the picking area is divided into several material levels;
[0053] S2: By observing and analyzing the distribution of materials in the retrieving area, manually select the material grabbing position and material discharging position on the man-machine interface;
[0054] S3: When the feeding port sends a feeding signal request, select the material grabbing position on the man-machine interface and click to confirm. The bridge frame and trolley of the bridge crane run to the material grabbing position at the same time, and the grab will automatically drop to the material level in the open state. After reaching the top of the material, the grab is closed while falling, and the grab slowly rises to the suspended state. After confirming that the grab weight setting condition is met, the grab quickly rises to the upp...
PUM
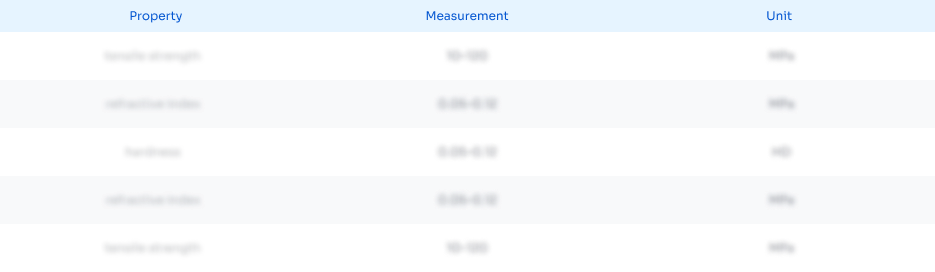
Abstract
Description
Claims
Application Information

- R&D Engineer
- R&D Manager
- IP Professional
- Industry Leading Data Capabilities
- Powerful AI technology
- Patent DNA Extraction
Browse by: Latest US Patents, China's latest patents, Technical Efficacy Thesaurus, Application Domain, Technology Topic, Popular Technical Reports.
© 2024 PatSnap. All rights reserved.Legal|Privacy policy|Modern Slavery Act Transparency Statement|Sitemap|About US| Contact US: help@patsnap.com