Gasoline-electric hybrid power matching method and system for a rotary wing aircraft
A technology of oil-electric hybrid power and aircraft, which is applied in the field of unmanned aerial vehicles, can solve the problems of short cruising distance, reduce motor, power waste, etc., and achieve the effect of increasing working life, improving flight efficiency and improving working conditions
- Summary
- Abstract
- Description
- Claims
- Application Information
AI Technical Summary
Problems solved by technology
Method used
Image
Examples
Embodiment 1
[0020] An oil-electric hybrid power matching method for a rotary wing aircraft, which uses a combination of an oil-powered engine and an electric motor as a power system, and adopts figure 1 In the parallel hybrid power transmission system shown, the oil-driven engine whose economical fuel consumption power meets the required power of the aircraft in the cruising phase is selected, and the electric motor power is the difference between the maximum required power of the aircraft and the maximum power of the oil-driven engine in the vertical take-off and landing phase. The parallel hybrid power transmission system includes: a transmission belt, a pulley (master and slave), a transmission shaft, a shaft coupling, a clutch, a speed reducer, and gears. The oil-powered engine transmits power to the main drive shaft through the drive belt. The front of the main transmission shaft is directly connected with the front pulling torque converter propeller, and the rear of the main transmi...
Embodiment 2
[0025] An oil-electric hybrid power system for a rotary wing aircraft, which consists of a main transmission chain from an oil-powered engine, an electric motor to a rotor, and a front transmission chain from an engine to a propeller. Power, the front transmission chain is used to provide power for the cruising flight of the aircraft, and the power transmitted by the front transmission chain during the vertical take-off and landing stage does not affect the vertical take-off and landing of the aircraft because the propeller blade angle is 0; A clutch is installed on the transmission chain. During the cruising phase, the motor stops working. The transmission chain between the oil-powered engine and the rotor cannot be transmitted to the rotor due to the disconnection of the clutch. The oil-driven engine only provides power for the front drive chain. At the same time, the propeller The blade angle is adjusted to the proper cruise driving angle. like figure 1 As shown, the main ...
PUM
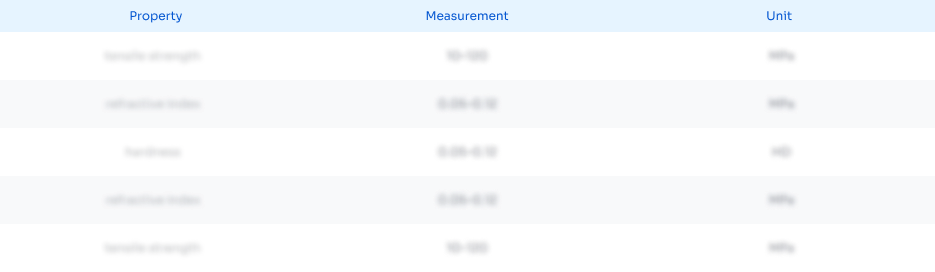
Abstract
Description
Claims
Application Information

- Generate Ideas
- Intellectual Property
- Life Sciences
- Materials
- Tech Scout
- Unparalleled Data Quality
- Higher Quality Content
- 60% Fewer Hallucinations
Browse by: Latest US Patents, China's latest patents, Technical Efficacy Thesaurus, Application Domain, Technology Topic, Popular Technical Reports.
© 2025 PatSnap. All rights reserved.Legal|Privacy policy|Modern Slavery Act Transparency Statement|Sitemap|About US| Contact US: help@patsnap.com