Aircraft skin clearance and scale measurement method based on parallel line structured light
A measurement method and structured light technology, applied in the field of image processing, can solve the problems of high measurement error, narrow application range, gap and step difference measurement, etc., to achieve the effect of low measurement error, wide application range and meeting measurement requirements
- Summary
- Abstract
- Description
- Claims
- Application Information
AI Technical Summary
Problems solved by technology
Method used
Image
Examples
Embodiment Construction
[0036] The present invention will be described in further detail below in conjunction with the accompanying drawings and specific embodiments.
[0037] Such as Figure 1-8 shown.
[0038] A method for measuring aircraft skin gaps and steps based on parallel line structured light, comprising the following steps:
[0039] (1) Calibration of structured light measurement system:
[0040] (1-1) Fix the position of the camera, the parallel line structured light emitter and the calibration plate, and collect the image of the calibration plate ( figure 1 ), extract the corner point image of the calibration board, and the corner points form two pairs of mutually orthogonal and three mutually parallel straight lines;
[0041] (1-2) Turn on the parallel line structured light emitter, project the structured light stripes on the calibration plate, extract the center of the structured light stripes, and calculate the intersection coordinates of the three parallel lines and the center lin...
PUM
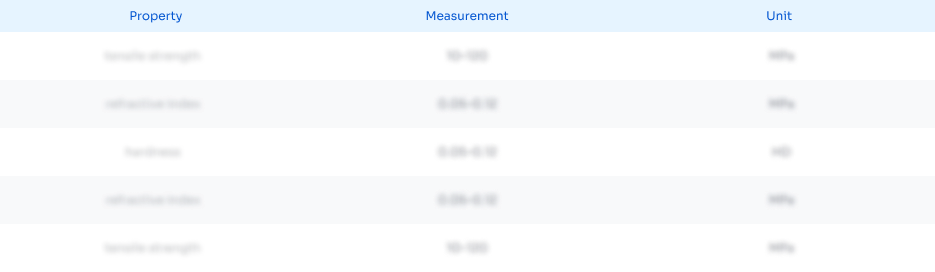
Abstract
Description
Claims
Application Information

- R&D
- Intellectual Property
- Life Sciences
- Materials
- Tech Scout
- Unparalleled Data Quality
- Higher Quality Content
- 60% Fewer Hallucinations
Browse by: Latest US Patents, China's latest patents, Technical Efficacy Thesaurus, Application Domain, Technology Topic, Popular Technical Reports.
© 2025 PatSnap. All rights reserved.Legal|Privacy policy|Modern Slavery Act Transparency Statement|Sitemap|About US| Contact US: help@patsnap.com