Method for extracting high-purity ethoxyquin by using multi-stage molecular distillation technology
A technology of ethoxyquinoline and molecular distillation, which is applied in the field of chemical industry and can solve the problems that separation technology is rarely reported.
- Summary
- Abstract
- Description
- Claims
- Application Information
AI Technical Summary
Problems solved by technology
Method used
Image
Examples
Embodiment 1
[0032] like image 3 As shown, the multi-stage molecular distillation extraction process flow is as follows: the crude ethoxyquinoline is filtered to remove particulate matter, and the obtained filtrate is transported to the primary molecular distillation raw material storage tank through a gear pump. The gear pump quantitatively transports 500mL of raw materials to the primary feeding tank. The raw materials are scraped on the inner wall of the distiller, evaporated, and condensed. The resulting heavy components enter the primary storage tank, and the light components are used as raw materials for secondary separation. By analogy, the raw materials are separated by secondary molecular distillation, the resulting light components enter the secondary storage tank, and the heavy components are used as raw materials for the tertiary separation. The raw materials are separated by three-stage molecular distillation, and the obtained light components are returned to the secondary fe...
Embodiment 2
[0038] like image 3 As shown, the multi-stage molecular distillation extraction process flow is as follows: the crude ethoxyquinoline is filtered to remove particulate matter, and the obtained filtrate is transported to the primary molecular distillation raw material storage tank through a gear pump. The gear pump quantitatively transports 500mL of raw materials to the primary feeding tank. The raw materials are scraped on the inner wall of the distiller, evaporated, and condensed. The resulting heavy components enter the primary storage tank, and the light components are used as raw materials for secondary separation. By analogy, the raw materials are separated by secondary molecular distillation, the resulting light components enter the secondary storage tank, and the heavy components are used as raw materials for the tertiary separation. The raw materials are separated by three-stage molecular distillation, and the obtained light components are returned to the secondary fe...
Embodiment 3
[0044] like image 3 As shown, the multi-stage molecular distillation extraction process flow is as follows: the crude ethoxyquinoline is filtered to remove particulate matter, and the obtained filtrate is transported to the primary molecular distillation raw material storage tank through a gear pump. The gear pump quantitatively transports 500mL of raw materials to the primary feeding tank. The raw materials scrape the film on the inner wall of the distiller, evaporate, and condense. The resulting heavy components enter the primary storage tank, and the light components are used as raw materials for secondary separation. By analogy, the raw materials are separated by secondary molecular distillation, the resulting light components enter the secondary storage tank, and the heavy components are used as raw materials for the tertiary separation. The raw materials are separated by three-stage molecular distillation, and the obtained light components are returned to the secondary ...
PUM
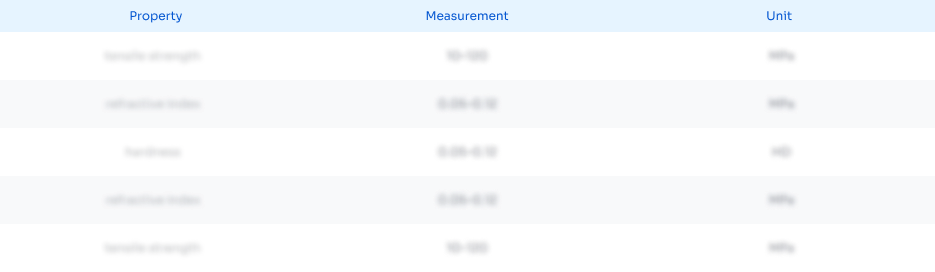
Abstract
Description
Claims
Application Information

- R&D
- Intellectual Property
- Life Sciences
- Materials
- Tech Scout
- Unparalleled Data Quality
- Higher Quality Content
- 60% Fewer Hallucinations
Browse by: Latest US Patents, China's latest patents, Technical Efficacy Thesaurus, Application Domain, Technology Topic, Popular Technical Reports.
© 2025 PatSnap. All rights reserved.Legal|Privacy policy|Modern Slavery Act Transparency Statement|Sitemap|About US| Contact US: help@patsnap.com