Robot welding path planning method based on firework particle swarm optimization algorithm
A technology of robot welding and particle swarm algorithm, which is applied in the direction of instruments, two-dimensional position/channel control, vehicle position/route/height control, etc., can solve the problems of slow algorithm convergence and time-consuming, and achieve optimal welding path and enhanced Population diversity, the effect of promoting optimization efficiency
- Summary
- Abstract
- Description
- Claims
- Application Information
AI Technical Summary
Problems solved by technology
Method used
Image
Examples
Embodiment Construction
[0018] The method of the present invention will be described in further detail below in conjunction with the accompanying drawings and embodiments.
[0019] A robot welding path planning method based on fireworks particle swarm algorithm, such as figure 1 shown, including the following steps:
[0020] Step S1: Use the greedy algorithm to initialize all path solutions and all control parameters of the population.
[0021] The specific method is as follows:
[0022] Step S1.1: Randomly select a welding point as the position Pwelding where the welding robot is located, and add the sequence of visited welding points;
[0023] Step S1.2: Search all the welding points that have not joined the visited sequence, find the welding point Pnext closest to the current welding robot position Pwelding, add it to the visited sequence as the current welding robot position. Repeat the above search until all the solder joints are added to the visited sequence, and a preliminary optimized indi...
PUM
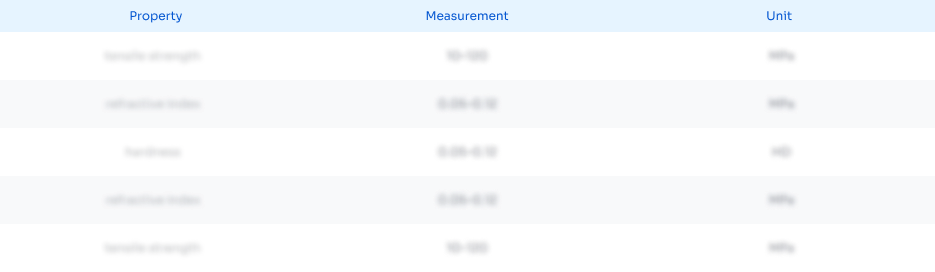
Abstract
Description
Claims
Application Information

- R&D Engineer
- R&D Manager
- IP Professional
- Industry Leading Data Capabilities
- Powerful AI technology
- Patent DNA Extraction
Browse by: Latest US Patents, China's latest patents, Technical Efficacy Thesaurus, Application Domain, Technology Topic, Popular Technical Reports.
© 2024 PatSnap. All rights reserved.Legal|Privacy policy|Modern Slavery Act Transparency Statement|Sitemap|About US| Contact US: help@patsnap.com