Feeding system applicable to super-large scale atomic layer deposition
An atomic layer deposition and feeding system technology, applied in the field of photovoltaic cell manufacturing and semiconductor manufacturing, can solve the problems of increasing the heating time of the product, the self-weight of the material chamber, and the lack of a uniform flow device in the intake air, so as to shorten the heating time and structure. Simple, uniform effect
- Summary
- Abstract
- Description
- Claims
- Application Information
AI Technical Summary
Problems solved by technology
Method used
Image
Examples
Embodiment
[0021] Embodiment: A feeding system suitable for ultra-large-scale atomic layer deposition, including a silicon wafer carrier 1 and a first end cap flange 2 and a second end cap method for clamping the silicon wafer carrier 1.
[0022] The silicon wafer carrier 1 includes several groups of carrier groups arranged side by side. Each carrier group is composed of multiple carriers. The carrier includes a carrier frame surrounded by two bottom plates and two side plates. The bottom plate and side plates of each carrier are connected end to end to form a hollow columnar structure; on the opposite sides of each carrier, there are several tooth slots evenly distributed from top to bottom on the opposite sides of each carrier. One correspondence, and the corresponding two teeth are located on the same plane, the corresponding two grooves on the two side plates carry two wafers, and the side of the two wafers to be coated faces outward, and the other side is attached to each other; Two wa...
PUM
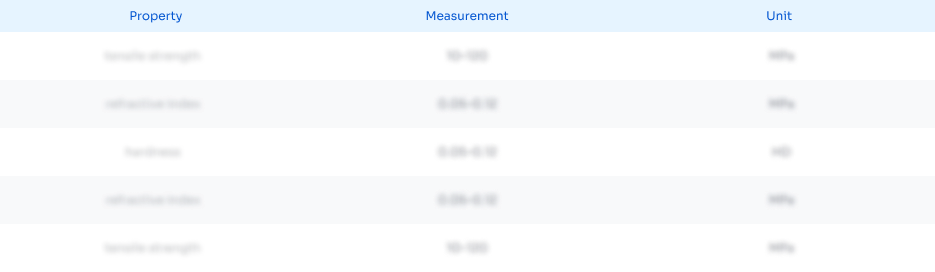
Abstract
Description
Claims
Application Information

- R&D Engineer
- R&D Manager
- IP Professional
- Industry Leading Data Capabilities
- Powerful AI technology
- Patent DNA Extraction
Browse by: Latest US Patents, China's latest patents, Technical Efficacy Thesaurus, Application Domain, Technology Topic, Popular Technical Reports.
© 2024 PatSnap. All rights reserved.Legal|Privacy policy|Modern Slavery Act Transparency Statement|Sitemap|About US| Contact US: help@patsnap.com