A fatigue deformation evolution model of concrete based on exponential Weibull equation
A fatigue deformation and evolution model technology, applied in electrical digital data processing, design optimization/simulation, special data processing applications, etc., can solve problems such as difficulty in popularization and application, complex model form, etc. easy-to-use effects
- Summary
- Abstract
- Description
- Claims
- Application Information
AI Technical Summary
Problems solved by technology
Method used
Image
Examples
Embodiment 1
[0022] This embodiment adopts the fatigue of the concrete compression fatigue sample D22 in "Fig.11" in the document "Holmen J O. Fatigue of concrete by constant and variable amplitude loading [J]. ACI Special Publication, 1982, 75:71-110." deformation result. The maximum deformation ε of the sample under compressive fatigue load s , Residual deformation ε p The evolution law of figure 1 shown. It should be noted that the maximum deformation ε of the fatigue specimen s Obtained directly from said literature, the residual deformation ε p Calculated from fatigue deformation results in the literature.
[0023] according to figure 1 The maximum deformation ε shown s The experimental value of , through fitting, the location parameter ε can be obtained s0 =0.09582, scale parameter λ s = 0.07378, the first shape parameter k s = 1.69074, the second shape parameter a s = 3.46586. Thus, the following fatigue deformation evolution model can be obtained:
[0024] n / N f =(1-e...
Embodiment 2
[0029] This embodiment adopts the literature "Chen X, Bu J, Fan X, et al. Effect of loading frequency and stress level on low cycle fatigue behavior of plain concrete in direct tension [J]. Construction and Building Materials, 2017, 133: 367-375 The fatigue deformation results of the concrete tensile fatigue specimen S=0.85test data in "Fig.8c" in ". The maximum deformation ε of the sample under the action of tensile fatigue load s , Residual deformation ε p The evolution law of figure 2 shown. It should be noted that the maximum deformation ε of the fatigue specimen s and residual deformation ε p were obtained directly from the literature.
[0030] according to figure 2The maximum deformation ε shown s The experimental value of , through fitting, the location parameter ε can be obtained s0 = 38.21874, scale parameter λ s = 70.86834, the first shape parameter k s =28.76554, the second shape parameter a s = 0.26049. Thus, the following fatigue deformation evolutio...
Embodiment 3
[0036] This embodiment adopts the literature "Liu W, Xu S, Li H.Flexural fatigue damage model of ultra-high toughness cementitious composites on base of continuum damagemechanics[J].International Journal of Damage Mechanics,2014,23(7):949-963 . "The fatigue deformation results of the fiber concrete bending fatigue specimen S0.80 in "Fig.3a". The maximum deformation ε of the sample under bending fatigue load s , Residual deformation ε p The evolution law of image 3 shown. It should be noted that the maximum deformation ε of the fatigue specimen s Obtained directly from said literature, the residual deformation ε p Calculated from fatigue deformation results in the literature.
[0037] according to image 3 The maximum deformation ε shown s The experimental value of , through fitting, the location parameter ε can be obtained s0 = 0.02474, scale parameter λ s = 2.83489, the first shape parameter k s =8.42487, the second shape parameter a s = 0.4282. Thus, the followi...
PUM
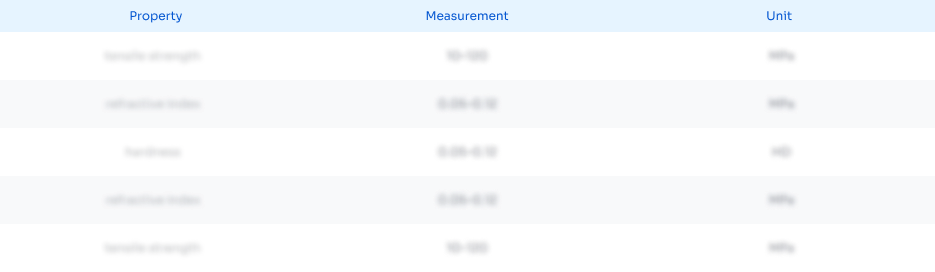
Abstract
Description
Claims
Application Information

- Generate Ideas
- Intellectual Property
- Life Sciences
- Materials
- Tech Scout
- Unparalleled Data Quality
- Higher Quality Content
- 60% Fewer Hallucinations
Browse by: Latest US Patents, China's latest patents, Technical Efficacy Thesaurus, Application Domain, Technology Topic, Popular Technical Reports.
© 2025 PatSnap. All rights reserved.Legal|Privacy policy|Modern Slavery Act Transparency Statement|Sitemap|About US| Contact US: help@patsnap.com