A Simultaneous Measurement Method of Internal Temperature and Wall Thickness of High-temperature Structures under Steady-state Conditions
A technology of internal temperature and steady-state conditions, applied in the direction of physical/chemical change thermometers, thermometers, heat measurement, etc., can solve the problems of increasing the difficulty of high-temperature thickness measurement, the difficulty of accurately describing gradient changes, and the inability to obtain accurate to-be-predicted values, etc. , to achieve the effect of solving the matrix singularity problem
- Summary
- Abstract
- Description
- Claims
- Application Information
AI Technical Summary
Problems solved by technology
Method used
Image
Examples
Embodiment Construction
[0029] In order to make the object, technical solution and advantages of the present invention clearer, the present invention will be further described in detail below in conjunction with the accompanying drawings and embodiments. It should be understood that the specific embodiments described here are only used to explain the present invention, not to limit the present invention.
[0030] The experiment adopts cylindrical 20# steel material specimen. A water-cooled heat exchanger is placed on the top of the specimen, while the bottom of the specimen is in contact with a flat heater for heating. After the non-uniform temperature field inside the test piece is stabilized (evaluated by the measured value of the thermocouple), the electromagnetic ultrasonic probe is placed on the top of the test piece, and the signal is excited / received once every 0.2s, and the average value of 10 times is taken as the acoustic sound under steady-state conditions. time measurement results. At t...
PUM
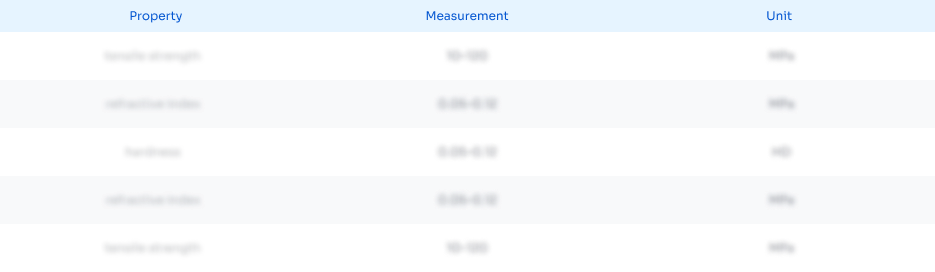
Abstract
Description
Claims
Application Information

- R&D
- Intellectual Property
- Life Sciences
- Materials
- Tech Scout
- Unparalleled Data Quality
- Higher Quality Content
- 60% Fewer Hallucinations
Browse by: Latest US Patents, China's latest patents, Technical Efficacy Thesaurus, Application Domain, Technology Topic, Popular Technical Reports.
© 2025 PatSnap. All rights reserved.Legal|Privacy policy|Modern Slavery Act Transparency Statement|Sitemap|About US| Contact US: help@patsnap.com