Method and clamp for machining thin-walled cylinder provided with groups of dense holes and oblique end faces
A technology of thin-walled cylinder and processing method, which is applied in the direction of manufacturing tools, metal processing equipment, household appliances, etc., can solve the problem of low utilization rate of parts and materials, achieve material cost saving, save equipment loss, and reduce processing preparation time Effect
- Summary
- Abstract
- Description
- Claims
- Application Information
AI Technical Summary
Problems solved by technology
Method used
Image
Examples
Embodiment Construction
[0028] Thin-walled cylindrical parts with densely clustered holes and inclined end faces are large in size, and there are hundreds of tiny cooling holes with a diameter of only 1mm distributed on the surface, and the design requires that the arrangement of these holes is symmetrically distributed along the axis of the part, but The number of small holes in each group is uneven. After technological tests, the present invention provides a laser processing method that completes all cooling holes and inclined end faces in one clamping. This process method can solve the problem of difficult alignment and positioning of the inclined end face, and at the same time, realize the one-time clamping processing of the air film group holes and the shape, thereby ensuring the design requirements of the position of the air film hole and the height dimension of the inclined end face.
[0029] A method for processing a thin-walled cylinder with densely clustered holes and inclined end faces of ...
PUM
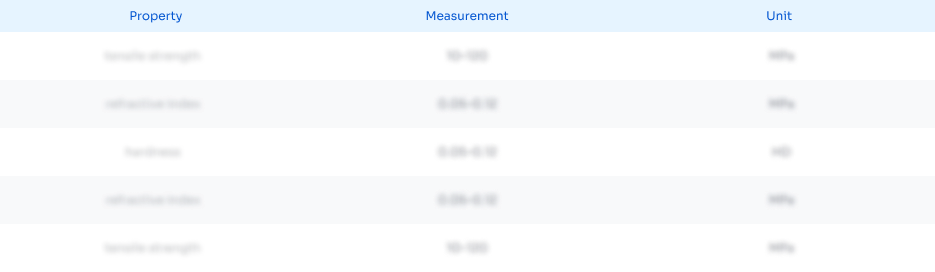
Abstract
Description
Claims
Application Information

- R&D
- Intellectual Property
- Life Sciences
- Materials
- Tech Scout
- Unparalleled Data Quality
- Higher Quality Content
- 60% Fewer Hallucinations
Browse by: Latest US Patents, China's latest patents, Technical Efficacy Thesaurus, Application Domain, Technology Topic, Popular Technical Reports.
© 2025 PatSnap. All rights reserved.Legal|Privacy policy|Modern Slavery Act Transparency Statement|Sitemap|About US| Contact US: help@patsnap.com