The multi-body dynamics model comprises an additional dummy and drive combined constraint construction method
A technology of multi-body dynamics and construction method, which is applied in the field of modeling and simulation of axisymmetric vector nozzle mechanism, and can solve problems such as loss of credibility of simulation results, imperfect functions, and inconsistent characteristics of load and force transmission.
- Summary
- Abstract
- Description
- Claims
- Application Information
AI Technical Summary
Problems solved by technology
Method used
Image
Examples
Embodiment Construction
[0022] The present invention will be described in detail below with reference to the accompanying drawings and examples.
[0023] The invention provides a method for constructing a combined constraint with additional dummy elements and drivers in a multibody dynamics model, comprising the following steps:
[0024] Step 1, expressing the convergent skeleton mid-surface curve of the axisymmetric vector nozzle in a parametric form;
[0025] Such as figure 1 As shown in Fig. 2(a) and (b), the spline curve of the surface curve in the convergent skeleton is obtained according to the discrete sampling of the analytical expression of the convergent skeleton working surface. The specific implementation is to use the macro command language of MSC.ADAMS to write the cyclic sampling code of the spline curve, to express the coordinates of the sampling coordinate points of the surface curve in the convergent skeleton in a parameterized way (stored with the MATRIX object), and then in the s...
PUM
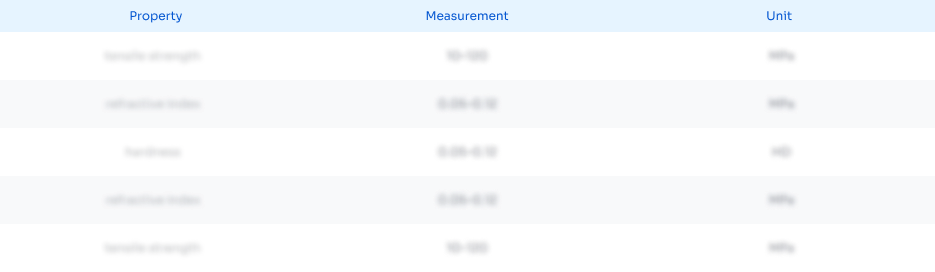
Abstract
Description
Claims
Application Information

- Generate Ideas
- Intellectual Property
- Life Sciences
- Materials
- Tech Scout
- Unparalleled Data Quality
- Higher Quality Content
- 60% Fewer Hallucinations
Browse by: Latest US Patents, China's latest patents, Technical Efficacy Thesaurus, Application Domain, Technology Topic, Popular Technical Reports.
© 2025 PatSnap. All rights reserved.Legal|Privacy policy|Modern Slavery Act Transparency Statement|Sitemap|About US| Contact US: help@patsnap.com