Method for monitoring vibration and strain of key position of cutter head system of full-section rock tunneling machine
A key position and strain monitoring technology, applied in earthwork drilling, mining equipment, tunnels, etc., can solve complex and changeable, troublesome measuring point layout, less research on vibration and strain monitoring schemes, etc., to prevent accidents , The effect of safe and reliable work
- Summary
- Abstract
- Description
- Claims
- Application Information
AI Technical Summary
Problems solved by technology
Method used
Image
Examples
Embodiment Construction
[0036] The specific implementation manner of the present invention will be described in detail below in conjunction with the accompanying drawings and technical solutions.
[0037] A method for monitoring vibration and strain at key positions of a cutter head system of a full-face rock excavator, the vibration and strain monitoring system at a key position of the cutter head system of a full-face rock excavator includes a sensor for measuring vibration, a sensor for measuring strain Strain gauges, wireless gateways that receive wireless signals, computers that display measurement data, layout models of key positions of the cutterhead system and spatial projection prediction models; monitor the operation process at corresponding positions through wireless sensors and strain gauges arranged at the easy-to-buy positions of the cutterhead system The state of vibration and strain in the TBM, while receiving and transmitting vibration and strain data based on the wireless network pro...
PUM
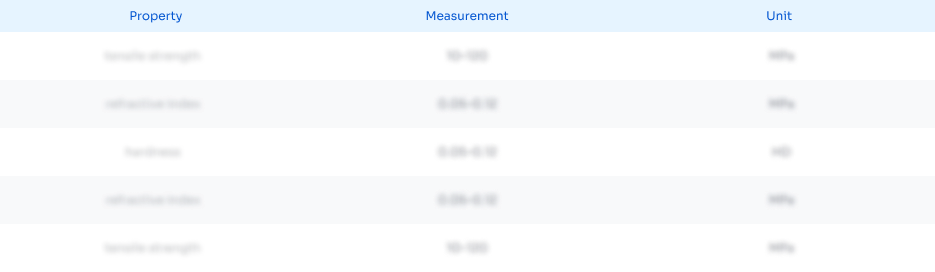
Abstract
Description
Claims
Application Information

- R&D
- Intellectual Property
- Life Sciences
- Materials
- Tech Scout
- Unparalleled Data Quality
- Higher Quality Content
- 60% Fewer Hallucinations
Browse by: Latest US Patents, China's latest patents, Technical Efficacy Thesaurus, Application Domain, Technology Topic, Popular Technical Reports.
© 2025 PatSnap. All rights reserved.Legal|Privacy policy|Modern Slavery Act Transparency Statement|Sitemap|About US| Contact US: help@patsnap.com