Large-scale mechanical automatic three-dimensional integral square knitting device
A large-scale mechanical and three-dimensional technology, applied in the field of three-dimensional weaving, can solve problems such as the inability to effectively improve the tightness and coordination of movements, the inability to guarantee the quality consistency of three-dimensional braided fabrics, increase the labor intensity and danger of workers, and achieve a simple structure. , the effect of uniform force and reducing labor intensity
- Summary
- Abstract
- Description
- Claims
- Application Information
AI Technical Summary
Problems solved by technology
Method used
Image
Examples
Embodiment 1
[0042] The present invention adopts the control mode of the terminal control machine 9, and the terminal control machine 9 is wired / wirelessly connected to the horizontal drive mechanism and the longitudinal drive mechanism, and is used to control the vertical drive mechanism to push the guide rail 5 to move along the longitudinal direction of the guide rail 5, and to control the horizontal drive mechanism to push the spindle 3. Movement in the chute; the movement of mounting table 1 on slide rail 1 and the movement of mounting table 2 on slide rail 3 can be realized by motor dragging mounting table 1 or mounting table 2, or installing a conveyor belt on the guide rail , The motor drives the conveyor belt to realize the movement of the first installation platform or the second installation platform. The terminal control machine 9 is provided with a touch screen for inputting and displaying the motion parameters of the horizontal drive mechanism and the longitudinal drive mechan...
Embodiment 2
[0044] The present invention can also adopt the mode of manually adjusting the displacement of the spindle and the guide rail. Four push switches 21 and four translation switches 22 are installed on the shell 2; each horizontal drive mechanism is respectively connected to a push switch 21 and a translation switch 22, and each longitudinal drive mechanism is also connected to a push switch 21 and a translation switch respectively 22. The push switch 21 is used to control the telescopic movement of the spindle 3 in the chute by the lateral drive mechanism, or to control the telescopic movement of the guide rail 5 along the longitudinal direction of the guide rail 5 by the longitudinal drive mechanism; the translation switch 22 is used to control the lateral drive mechanism along the guide rail. 5 translational movement in the longitudinal direction, or control the translational movement of the longitudinal drive mechanism along the transverse direction of the guide rail 5 . The ...
PUM
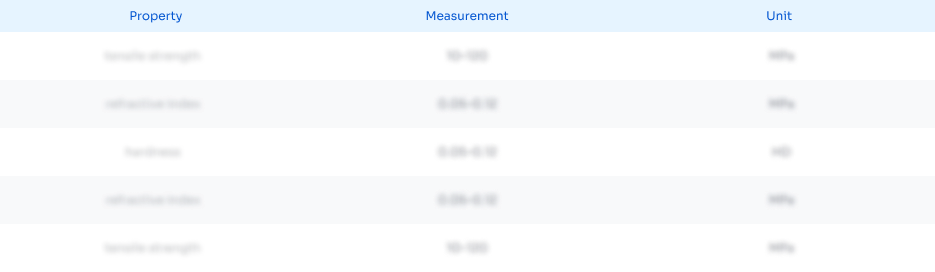
Abstract
Description
Claims
Application Information

- R&D
- Intellectual Property
- Life Sciences
- Materials
- Tech Scout
- Unparalleled Data Quality
- Higher Quality Content
- 60% Fewer Hallucinations
Browse by: Latest US Patents, China's latest patents, Technical Efficacy Thesaurus, Application Domain, Technology Topic, Popular Technical Reports.
© 2025 PatSnap. All rights reserved.Legal|Privacy policy|Modern Slavery Act Transparency Statement|Sitemap|About US| Contact US: help@patsnap.com