Nylon yarn-dyed weaving raw yarn warping method
A raw yarn and nylon technology, applied in the warping field of nylon yarn-dyed raw yarn, can solve the problems of large production waste, low production efficiency of dyed yarn warping, warp color difference, etc., achieve uniform density, improve dyeing quality and weaving efficiency , The effect of smooth warping yarn
- Summary
- Abstract
- Description
- Claims
- Application Information
AI Technical Summary
Problems solved by technology
Method used
Image
Examples
Embodiment 1
[0017] Example 1: 1400 meters, 500 heads, uniaxial weight 7kg*10 pieces
[0018] Stainless steel warp beams are used, and the shaft disks of the warp beams are waxed. The warp yarn paper tubes are made of seamless paper tubes with tube heads, and the warping machines are selected for batch warping machines. The warping steps are:
[0019] (1) Spun nylon raw yarn into compact warp yarn, the speed of the vehicle is 550m / min, the original yarn and the compact warp yarn are vertical to the center line, and the distance between the two is 95cm;
[0020] (2) Carry out warping production in sequence, and the tight warp yarn density is 400g / dm 3 , the creel and the hanging warp yarns are in a parallel state, and the talcum powder is rubbed by hand, and the yarn humidity is 63% when the car is worn;
[0021] (3) Swing the reed, put every 9 yarns into the reed teeth in a row, each reed tooth needle is extended sequentially at a distance of 2mm, and the reed tooth needle is wiped with ...
Embodiment example 2
[0025] Implementation case 2: 2800 meters, 600 heads, single shaft weight 18kg*8
[0026] Stainless steel warp beams are used, and the shaft disks of the warp beams are waxed. The warp yarn paper tubes are made of seamless paper tubes with tube heads, and the warping machines are selected for batch warping machines. The warping steps are:
[0027] (1) Spin nylon raw yarn into compact warp yarn at a speed of 600m / min, the original yarn and the compact warp yarn are vertical to the center line, and the distance between the two is 100cm;
[0028] (2) Carry out warping production in sequence, and the tight warp yarn density is 430g / dm 3 , the creel is in a parallel state with the warp yarns hung, rubbed with talcum powder by hand, and the yarn humidity is 65% when worn;
[0029] (3) Swing the reed, put every 9 yarns into the reed teeth in a row, each reed tooth needle is extended sequentially at a distance of 2mm, and the reed tooth needle is wiped with talcum powder;
[0030] ...
Embodiment example 3
[0033] Implementation case three: 4000 meters, 700 heads, uniaxial weight 26kg*6
[0034] Stainless steel warp beams are used, and the shaft disks of the warp beams are waxed. The warp yarn paper tubes are made of seamless paper tubes with tube heads, and the warping machines are selected for batch warping machines. The warping steps are:
[0035] (1) Spin nylon raw yarn into tight warp yarn, the speed of the vehicle is 650m / min, the original yarn and tight warp yarn are vertical center line, and the distance between the two is 104cm;
[0036] (2) Carry out warping production in sequence, and the tight warp yarn density is 450g / dm 3 , the creel and the hanging warp yarns are in a parallel state, and the talcum powder is rubbed by hand, and the yarn humidity is 68% when the car is worn;
[0037] (3) Swing the reed, put every 9 yarns into the reed teeth in a row, each reed tooth needle is extended sequentially at a distance of 2mm, and the reed tooth needle is wiped with talcu...
PUM
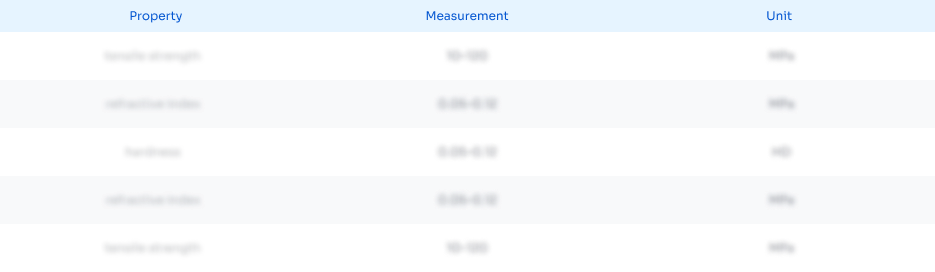
Abstract
Description
Claims
Application Information

- Generate Ideas
- Intellectual Property
- Life Sciences
- Materials
- Tech Scout
- Unparalleled Data Quality
- Higher Quality Content
- 60% Fewer Hallucinations
Browse by: Latest US Patents, China's latest patents, Technical Efficacy Thesaurus, Application Domain, Technology Topic, Popular Technical Reports.
© 2025 PatSnap. All rights reserved.Legal|Privacy policy|Modern Slavery Act Transparency Statement|Sitemap|About US| Contact US: help@patsnap.com