A Synchronous Extrusion Forming Method for "h" Shape Connectors Made of Steel with Different Wall Thickness
A technology of simultaneous extrusion and connecting parts, applied in the direction of metal extrusion dies, metal extrusion mandrels, etc., to achieve the effects of increased applicability, optimal comprehensive mechanical properties, and good metal stress state
- Summary
- Abstract
- Description
- Claims
- Application Information
AI Technical Summary
Problems solved by technology
Method used
Image
Examples
Embodiment Construction
[0035] The present invention discloses a method for synchronous extrusion forming of "H"-shaped connectors made of steel with different wall thicknesses. Figure 1-13 , the mold includes an upper mold assembly connected to the upper part of the press, a lower mold assembly connected to the lower part of the press, and a guide and ejector assembly.
[0036] Such as figure 1As shown, the shown upper mold assembly includes: an upper template 18 connected with the upper workbench of the press, an insert 20 and an upper mold base 17 connected with the upper template 18, a punch 13 connected with the insert 20 and The upper mold cover plate 21, and the coil 15 and the return ring 14 connected with the upper mold base 17. The insert 20 is built into the upper mold base 17, the coil 15 is ring-sleeved under the upper mold base 17, the punch 13 passes through the upper mold base 17 and the coil 15, and the upper mold cover plate 21 is placed between the upper mold base 17 and the pun...
PUM
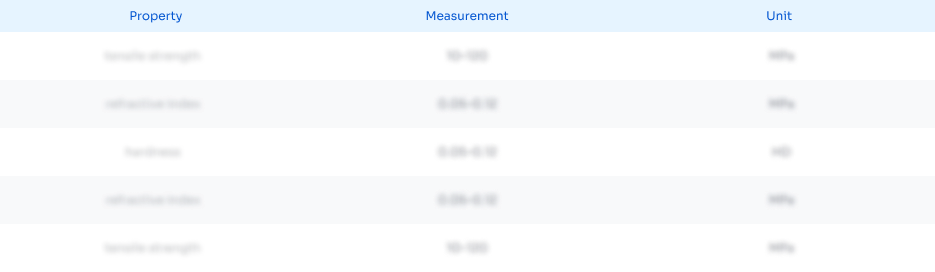
Abstract
Description
Claims
Application Information

- R&D
- Intellectual Property
- Life Sciences
- Materials
- Tech Scout
- Unparalleled Data Quality
- Higher Quality Content
- 60% Fewer Hallucinations
Browse by: Latest US Patents, China's latest patents, Technical Efficacy Thesaurus, Application Domain, Technology Topic, Popular Technical Reports.
© 2025 PatSnap. All rights reserved.Legal|Privacy policy|Modern Slavery Act Transparency Statement|Sitemap|About US| Contact US: help@patsnap.com