A Calibration Method of Entrance Guide Wheel in Finish Rolling
A calibration method and imported technology, applied in the field of steel rolling process, can solve the problems of long time, center line position deviation, large deviation, etc., and achieve the effect of improving safety factor, reducing workload and ensuring rolling stability
- Summary
- Abstract
- Description
- Claims
- Application Information
AI Technical Summary
Problems solved by technology
Method used
Image
Examples
Embodiment
[0032] The fixed distance L between the inside of the rolling mill archway and the center line of the rolling mill: 1000mm.
[0033] Entrance guide width L2: 320mm.
[0034] The guide wheel exceeds the width L3 of the guide bar: 10mm.
[0035] F1~F7 guide wheel calibration comparison table is as follows:
[0036] F1~F7 guide wheel calibration conversion table
[0037]
[0038]
[0039] F1 guide wheel calibration, at the entrance of the rolling mill, measure the shortest distance L1 from the inner side of the rolling mill archway on the working side close to the guide bar transmission device to the outer side of the entrance guide bar, which is 160mm; according to the comparison table, check the distance from the working side guide wheel to the rolling center line The distance (that is, the calibration distance of the guide wheel) L4 is 510mm, and then the guide wheel is calibrated in the first-level screen of the console.
[0040] Measure the shortest distance L1 from...
PUM
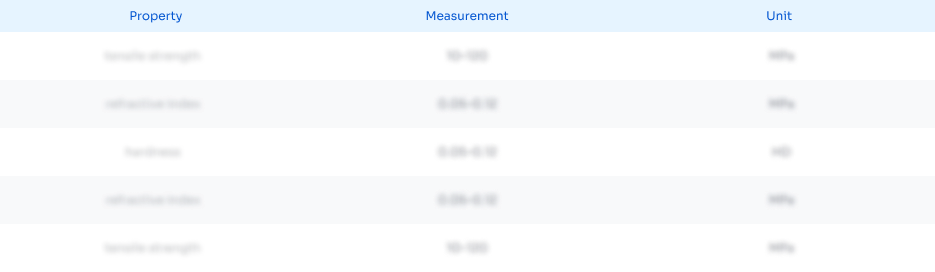
Abstract
Description
Claims
Application Information

- R&D
- Intellectual Property
- Life Sciences
- Materials
- Tech Scout
- Unparalleled Data Quality
- Higher Quality Content
- 60% Fewer Hallucinations
Browse by: Latest US Patents, China's latest patents, Technical Efficacy Thesaurus, Application Domain, Technology Topic, Popular Technical Reports.
© 2025 PatSnap. All rights reserved.Legal|Privacy policy|Modern Slavery Act Transparency Statement|Sitemap|About US| Contact US: help@patsnap.com