Multi-robot cooperative sorting method and system
A multi-robot and robot technology, applied in the field of visual sorting, can solve the problems of high miss rate, affecting sorting efficiency, unreasonable sorting strategy, etc., and achieve the effect of improving position accuracy and improving sorting efficiency
- Summary
- Abstract
- Description
- Claims
- Application Information
AI Technical Summary
Problems solved by technology
Method used
Image
Examples
Embodiment Construction
[0025] In order to further understand the content, features and effects of the present invention, the following embodiments are given as examples, and detailed descriptions are as follows with accompanying drawings:
[0026] See figure 1 with figure 2 , A multi-robot collaborative sorting method of the present invention includes the following steps:
[0027] (1) The camera 1 is installed on the conveyor belt 3 and located upstream of the parallel robot 6. The camera 1 is perpendicular to the conveyor belt 3, and multiple parallel robots are installed on the conveyor downstream of the camera through brackets. Above the conveyor belt 3 and the feeding conveyor belt 4, install an encoder on the left end of the plane of the conveyor belt 3, and then start the conveyor belt 3 to drive the workpiece. The upper computer 5 converts the image of the workpiece collected by the camera 1 into a grayscale image, and then further processing Obtain the contour information of the workpiece;
[002...
PUM
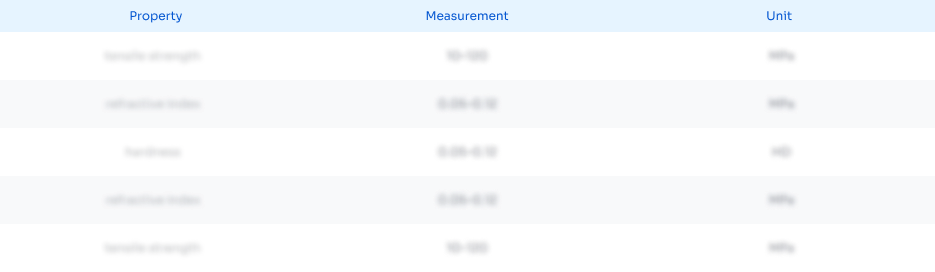
Abstract
Description
Claims
Application Information

- R&D
- Intellectual Property
- Life Sciences
- Materials
- Tech Scout
- Unparalleled Data Quality
- Higher Quality Content
- 60% Fewer Hallucinations
Browse by: Latest US Patents, China's latest patents, Technical Efficacy Thesaurus, Application Domain, Technology Topic, Popular Technical Reports.
© 2025 PatSnap. All rights reserved.Legal|Privacy policy|Modern Slavery Act Transparency Statement|Sitemap|About US| Contact US: help@patsnap.com