Forming mold and forming method for fiber cloth curved surface prefabricated member
A forming mold and forming method technology, which is applied in the forming mold and forming field of fiber cloth curved surface prefabricated parts, can solve the problems of curved surface prefabricated parts forming, etc., and achieve the effects of uniform density, saving usage, and small shaping error
- Summary
- Abstract
- Description
- Claims
- Application Information
AI Technical Summary
Problems solved by technology
Method used
Image
Examples
Embodiment Construction
[0049] The following is attached Figure 1-8 An embodiment of the present invention will be described.
[0050] The fiber cloth curved surface prefabricated mold of the present invention comprises an inner mold 1, an outer mold 2 and four clamping lugs 4; the clamping lugs 4 comprise a connected connection part 41 and a positioning part 42, and the connection part 41 is fixedly arranged on The end of the inner mold 1 or the outer mold 2; the bottom surface of the positioning part 42 is a positioning surface, which is used to ensure uniform thickness of the fiber cloth curved surface preform; the lower bottom surface of the clamping ear piece 4 is provided with a groove 43 for accommodating excess fiber cloth . The inner mold 1 and the outer mold 2 are provided with a plurality of ventilation holes 5 corresponding to each other and evenly arranged. The diameter of the plurality of ventilation holes is 7 mm, and the plurality of ventilation holes are arranged in a circular arra...
PUM
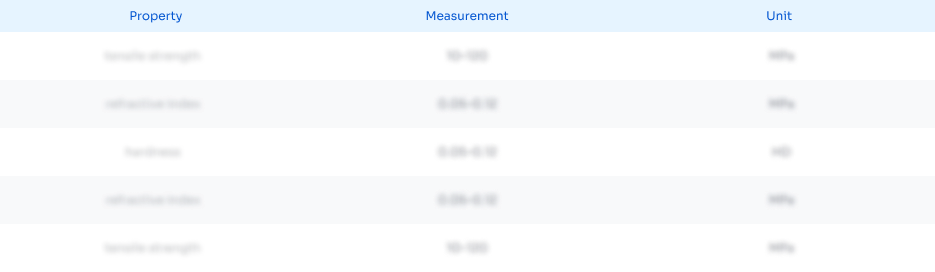
Abstract
Description
Claims
Application Information

- R&D
- Intellectual Property
- Life Sciences
- Materials
- Tech Scout
- Unparalleled Data Quality
- Higher Quality Content
- 60% Fewer Hallucinations
Browse by: Latest US Patents, China's latest patents, Technical Efficacy Thesaurus, Application Domain, Technology Topic, Popular Technical Reports.
© 2025 PatSnap. All rights reserved.Legal|Privacy policy|Modern Slavery Act Transparency Statement|Sitemap|About US| Contact US: help@patsnap.com