An Efficient Parallel Layer Slicing Method for STL Models Based on Co-point Welding Sorting
A layer-cutting and model-based technology, applied in the field of additive manufacturing, can solve problems such as reduced layer-cutting efficiency and complex model-cutting accuracy, and achieve the effects of reducing construction time, improving layer-cutting efficiency, and improving layer-cutting efficiency
- Summary
- Abstract
- Description
- Claims
- Application Information
AI Technical Summary
Problems solved by technology
Method used
Image
Examples
Embodiment Construction
[0024] In order to illustrate the technical scheme and technical purpose of the present invention, the present invention will be further introduced below in conjunction with the accompanying drawings and specific embodiments.
[0025] combine figure 1 , a kind of STL model high-efficiency parallel layer-slicing method based on co-point welding sorting of the present invention, comprises the following steps:
[0026] Step 1. Read the STL model and construct the index information of the vertices and edges of the triangle face
[0027] 1.1. Create a storage container:
[0028] Create an associative container PointToIndex for storing vertices and vertex indexes, and an associative container EdgeToIndex for storing edges and edge indexes. The two associative containers are initially empty, that is, no elements are stored. In addition, to store the coordinates of the three vertices of the triangular patch (P 1 ,P 2 ,P 3 ), the indices of the three vertices (PIndex 1 、PIndex 2...
PUM
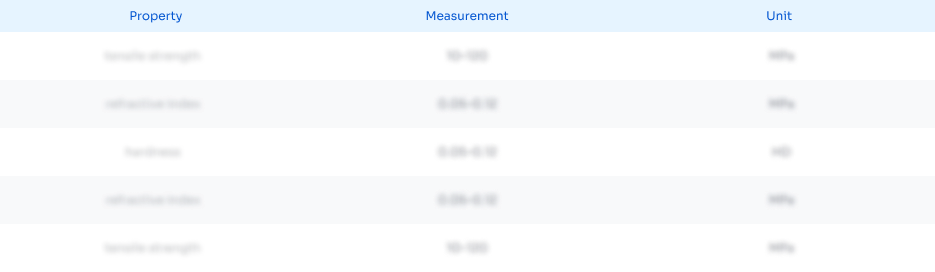
Abstract
Description
Claims
Application Information

- Generate Ideas
- Intellectual Property
- Life Sciences
- Materials
- Tech Scout
- Unparalleled Data Quality
- Higher Quality Content
- 60% Fewer Hallucinations
Browse by: Latest US Patents, China's latest patents, Technical Efficacy Thesaurus, Application Domain, Technology Topic, Popular Technical Reports.
© 2025 PatSnap. All rights reserved.Legal|Privacy policy|Modern Slavery Act Transparency Statement|Sitemap|About US| Contact US: help@patsnap.com