A precise three-dimensional measurement method based on line-structured light-driven holographic interferometry
A holographic interference and line structured light technology, applied in the field of precision measurement, can solve the problems of coordinate system registration troubled by rapid and precise detection of parts, and achieve the effect of reducing the difficulty of clamping and positioning
- Summary
- Abstract
- Description
- Claims
- Application Information
AI Technical Summary
Problems solved by technology
Method used
Image
Examples
Embodiment Construction
[0018] The working principle of the measurement method of the present invention is as follows: first, the global coordinate system calibration of the line structured light sensor and the holographic interference sensor is carried out, so that the line structured light vision sensor and the holographic interference sensor work in the same coordinate system; For example, fast scanning measurement of turbine blades, multiple linear 3D point cloud data of parts are obtained, curve fitting and data processing are performed on the point cloud data, and holographic interferometric measurement paths are generated. The four-axis control system drives the holographic interferometric sensor according to the generated The path is finely measured, and the complete high-precision point cloud data of the part is finally obtained.
[0019] A precision three-dimensional measurement method for line-structured light-driven holographic interferometry, which uses four-axis linkage equipment to plan...
PUM
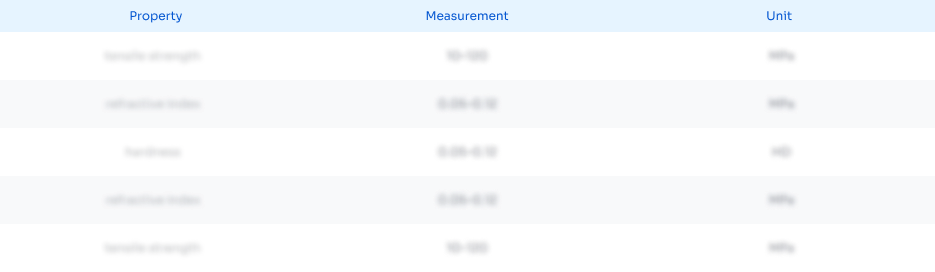
Abstract
Description
Claims
Application Information

- R&D
- Intellectual Property
- Life Sciences
- Materials
- Tech Scout
- Unparalleled Data Quality
- Higher Quality Content
- 60% Fewer Hallucinations
Browse by: Latest US Patents, China's latest patents, Technical Efficacy Thesaurus, Application Domain, Technology Topic, Popular Technical Reports.
© 2025 PatSnap. All rights reserved.Legal|Privacy policy|Modern Slavery Act Transparency Statement|Sitemap|About US| Contact US: help@patsnap.com