Damping thrust bearing with static water thrust self-balance function
A thrust bearing and self-balancing technology, applied in the direction of rotating bearings, bearings, bearing components, etc., can solve the problem of load-bearing performance and reliability of vibration-damping components, reduce the effective use range of vibration-damping technology, and endanger the safety of propellers, etc. problem, to achieve the effect of increasing the natural frequency ratio of the shafting, stable stiffness and high reliability
- Summary
- Abstract
- Description
- Claims
- Application Information
AI Technical Summary
Problems solved by technology
Method used
Image
Examples
Embodiment Construction
[0027] The present invention will be further described below in conjunction with the drawings and examples. The specific implementation of the patent of the present invention is shown in the attached figure 1 ~ attached image 3 , the present invention will be further described below in conjunction with accompanying drawing.
[0028] A vibration-damping thrust bearing with hydrostatic thrust self-balancing function installed on the main propulsion shaft system of the present invention, comprising a thrust shaft 1, a housing 2, a reverse vibration-damping cylinder 3, a thrust block 4, a supporting stationary ring 5, and a front wheel Damping cylinder 6, supporting bearing bush 7, hydraulic pipeline 8, seawater pressure compensator 9 and end face oil seal, etc. It is used for self-balancing during the operation of the propeller shaft system.
[0029] The layout of each component is shown in the appendix figure 1 : The thrust shaft 1 is installed in the center of the housing ...
PUM
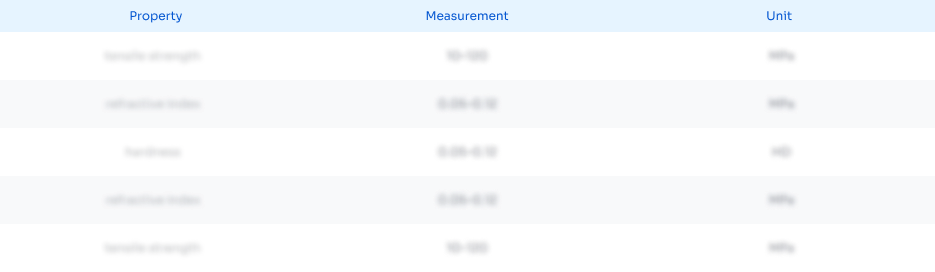
Abstract
Description
Claims
Application Information

- R&D
- Intellectual Property
- Life Sciences
- Materials
- Tech Scout
- Unparalleled Data Quality
- Higher Quality Content
- 60% Fewer Hallucinations
Browse by: Latest US Patents, China's latest patents, Technical Efficacy Thesaurus, Application Domain, Technology Topic, Popular Technical Reports.
© 2025 PatSnap. All rights reserved.Legal|Privacy policy|Modern Slavery Act Transparency Statement|Sitemap|About US| Contact US: help@patsnap.com