Disc type brake device structure in robot joint module
A technology for robot joints and braking devices, which is applied to manipulators, manufacturing tools, etc., can solve the problems of high brake cost, low braking precision, and small torque, and achieve the effect of low component cost and stable and reliable braking performance.
- Summary
- Abstract
- Description
- Claims
- Application Information
AI Technical Summary
Problems solved by technology
Method used
Image
Examples
Embodiment Construction
[0018] In order to make the present invention more comprehensible, preferred embodiments are described in detail below with accompanying drawings.
[0019] Such as Figure 1 to Figure 2 As shown, in order to use the traditional power-off brake to produce the braking effect by utilizing the mechanical action of the coil to be adsorbed on the spring, a disc brake device structure in the robot joint module is designed, which includes the motor rotor 8 Hollow motor shaft 3, one side of the motor rotor 8 is provided with a brake groove 6 sleeved on the hollow motor shaft 3, and the brake groove 6 includes a restricting shaft sleeved outside the hollow motor shaft 3 and arranged on The restriction surface on one side of the motor rotor 8, the restriction shaft of the braking groove 6 is provided with a sliding braking component 5, and the sliding braking component 5 includes a sliding shaft and a vertical On the sliding restriction surface of the sliding shaft, the sliding restrict...
PUM
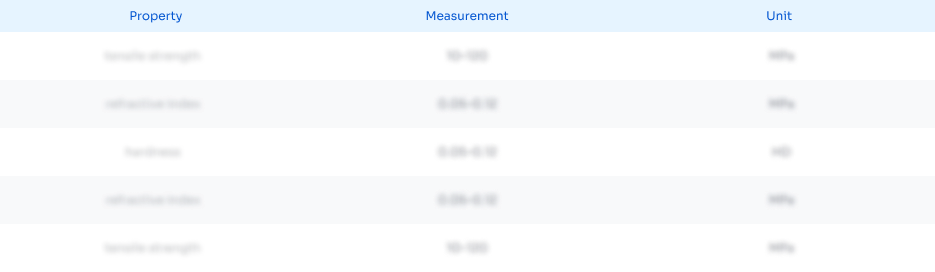
Abstract
Description
Claims
Application Information

- R&D Engineer
- R&D Manager
- IP Professional
- Industry Leading Data Capabilities
- Powerful AI technology
- Patent DNA Extraction
Browse by: Latest US Patents, China's latest patents, Technical Efficacy Thesaurus, Application Domain, Technology Topic, Popular Technical Reports.
© 2024 PatSnap. All rights reserved.Legal|Privacy policy|Modern Slavery Act Transparency Statement|Sitemap|About US| Contact US: help@patsnap.com