A method for directly repairing lithium iron phosphate waste powder by fire method to prepare battery-grade lithium iron phosphate
A lithium iron phosphate, battery-grade technology, which is applied in the field of directly repairing lithium iron phosphate waste powder to prepare battery-grade lithium iron phosphate by fire method, can solve the problems of low economic value, high processing cost, long process, etc., to eliminate pollution and application. The effect of broad prospects and a large amount of recycling
- Summary
- Abstract
- Description
- Claims
- Application Information
AI Technical Summary
Problems solved by technology
Method used
Image
Examples
Embodiment 1
[0045] like Figure 5 As shown, a method for directly repairing lithium iron phosphate waste powder fire method to prepare battery-grade lithium iron phosphate comprises the following steps:
[0046] Step A, oxidative roasting, put the ceramic crucible containing 15 kg of lithium iron phosphate positive electrode material into a roasting furnace, and roast it under air atmosphere conditions, the roasting temperature is 650 ° C, and the roasting time is 15 hours to obtain calcined sand. SEM picture of calcined sand figure 1 shown.
[0047] Step B, batching, add lithium source, iron source, phosphorus source to the calcined sand obtained in step A, make the molar ratio of lithium, iron, phosphorus in the calcined sand be adjusted to 1.03:1:1, add carbon source and As for the activator glycerin, the mass of the added carbon source is 18% of the mass of the calcine, and the mass of the added activator glycerin is 2% of the mass of the calcine. Wherein, the lithium source is lit...
Embodiment 2
[0053] A method for directly repairing and preparing battery-grade lithium iron phosphate by the fire method of waste powder of lithium iron phosphate comprises the following steps:
[0054] Step A, oxidative roasting, put a ceramic crucible containing 15 kg of lithium iron phosphate waste powder into a roasting furnace, and roast under an oxygen atmosphere at a roasting temperature of 850° C. for 6 hours to obtain calcined sand.
[0055] Step B, batching, add lithium source, iron source, phosphorus source to the calcined sand obtained in step A, adjust the molar ratio of lithium, iron, phosphorus in the calcined sand to 1.06:1:1, and then add starch and activator Glycerol, the quality that described starch adds is 16% of the quality of calcine, and the quality that described activator glycerin adds is 4% of the quality of calcine; Wherein, described lithium source is lithium carbonate, hydroxide Lithium, lithium oxalate, etc.; iron source is iron oxide, iron sulfate, etc.; ph...
Embodiment 3
[0061] A method for directly repairing and preparing battery-grade lithium iron phosphate by the fire method of waste powder of lithium iron phosphate comprises the following steps:
[0062] Step A, oxidation roasting, put the ceramic crucible equipped with 15 kg of lithium iron phosphate positive electrode separation material into the roasting furnace, and roast under the atmosphere of air, the roasting temperature is 750 ° C, and the roasting time is 10 hours to obtain calcined sand.
[0063] Step B, ingredients, add lithium source, iron source, phosphorus source to the calcined sand obtained in step A, adjust the molar ratio of lithium, iron, phosphorus in the calcined sand to 1.05:1:1, then add sucrose and activator Glycerol, the quality that described sucrose adds is 17% of the quality of calcine, and the quality that described activator glycerin adds is 3% of the quality of calcine. Wherein, the lithium source is lithium carbonate, lithium hydroxide, lithium oxalate, etc...
PUM
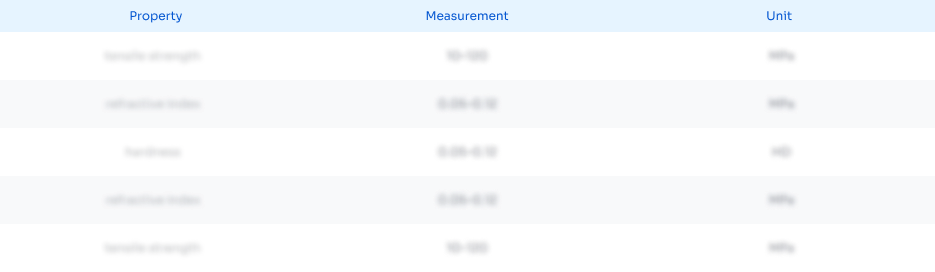
Abstract
Description
Claims
Application Information

- R&D
- Intellectual Property
- Life Sciences
- Materials
- Tech Scout
- Unparalleled Data Quality
- Higher Quality Content
- 60% Fewer Hallucinations
Browse by: Latest US Patents, China's latest patents, Technical Efficacy Thesaurus, Application Domain, Technology Topic, Popular Technical Reports.
© 2025 PatSnap. All rights reserved.Legal|Privacy policy|Modern Slavery Act Transparency Statement|Sitemap|About US| Contact US: help@patsnap.com