Production method of non-oriented electrical steel hot rolled plate
A technology of grain-oriented electrical steel and production method, applied in the field of metallurgy, can solve the problems of difficulty in tapping, reduce production efficiency, affect the shape, thickness accuracy and performance of non-oriented electrical steel hot-rolled sheets, and achieve great promotion and application prospects. cost reduction effect
- Summary
- Abstract
- Description
- Claims
- Application Information
AI Technical Summary
Problems solved by technology
Method used
Examples
Embodiment 1
[0016] The molten steel is smelted through the ordinary steel production line, and the molten steel is cast into a slab. The length of the slab is 9800mm, and the thickness of the slab is 160mm. The slab is heated in the heating furnace, and the temperature of the slab entering the preheating section of the heating furnace is The temperature of the slab is 210°C. The slab is heated to 1000°C in the preheating section and 1250°C in the heating section. The temperature of the slab in the rough rolling process is 1230°C. The rough rolling process adopts high-speed rolling. Descaling to obtain an intermediate slab with a thickness of 40mm, the temperature of the intermediate slab entering the finish rolling process is 1020°C, the exit speed of the finish rolling process is m / s, the temperature of the finish rolled plate obtained by the finish rolling process is 880°C, and the thickness is 2.6 mm, after testing, the Si content in the obtained hot-rolled sheet of non-oriented electri...
Embodiment 2
[0019] The molten steel is smelted through the ordinary steel production line, and the molten steel is cast into a slab. The length of the slab is 9700mm, and the thickness of the slab is 200mm. The slab is heated in the heating furnace, and the temperature of the slab entering the preheating section of the heating furnace is The temperature of the slab is 360°C. The slab is heated to 980°C in the preheating section, and is released after being heated to 1120°C in the heating section. The temperature of the slab in the rough rolling process is 1100°C. The rough rolling process uses high-speed rolling. Descaling to obtain an intermediate slab with a thickness of 38mm, the temperature of the intermediate slab entering the finish rolling process is 980°C, the exit speed of the finish rolling process is 9m / s, the temperature of the finish rolled plate obtained by the finish rolling process is 850°C, and the thickness is 2.0mm, after detection, the content of Si in the obtained hot-...
Embodiment 3
[0022] The molten steel is smelted through the ordinary steel production line, and the molten steel is cast into a slab. The length of the slab is 10,000mm, and the thickness of the slab is 240mm. The slab is heated in the heating furnace, and the temperature of the slab entering the preheating section of the heating furnace is The temperature of the slab is 330°C. The slab is heated to 1050°C in the preheating section, and is released after being heated to 1200°C in the heating section. The temperature of the slab in the rough rolling process is 1180°C. The rough rolling process adopts high-speed rolling. Descaling to obtain an intermediate slab with a thickness of 36mm, the temperature of the intermediate slab entering the finish rolling process is 1000°C, the exit speed of the finish rolling process is 14m / s, the temperature of the finish rolled plate obtained by the finish rolling process is 850°C, and the thickness is 3.0 mm, after testing, the Si content in the obtained h...
PUM
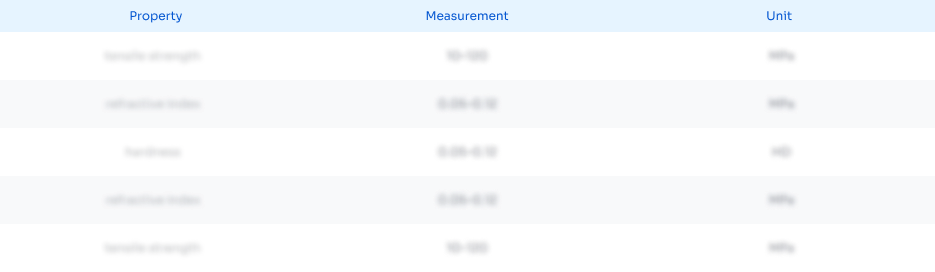
Abstract
Description
Claims
Application Information

- R&D
- Intellectual Property
- Life Sciences
- Materials
- Tech Scout
- Unparalleled Data Quality
- Higher Quality Content
- 60% Fewer Hallucinations
Browse by: Latest US Patents, China's latest patents, Technical Efficacy Thesaurus, Application Domain, Technology Topic, Popular Technical Reports.
© 2025 PatSnap. All rights reserved.Legal|Privacy policy|Modern Slavery Act Transparency Statement|Sitemap|About US| Contact US: help@patsnap.com