Irregular composite battery box forming die and forming method
A composite material and molding die technology, used in household appliances, other household appliances, household components, etc., can solve the problems of poor product stability and uneven force, achieve good appearance, eliminate uneven force, and improve molding. The effect of pass rate
- Summary
- Abstract
- Description
- Claims
- Application Information
AI Technical Summary
Problems solved by technology
Method used
Image
Examples
Embodiment 1
[0047] Step 1. Treat the mold: use the mold release agent to wipe the inner surface of the mold body 1 three times, and dry it after each wipe. The interval between each wipe is 5 minutes, and the cumulative thickness of the mold release agent is 0.1mm.
[0048] Step 2, continuous fiber prepreg layering: 12 layers of continuous fiber prepreg are selected for orderly layering on the surface of the mold body 1, and the cumulative thickness is 3 mm to form a prepreg layer 2.
[0049] Step 3, adding auxiliary materials: laying a release cloth and a vacuum film 4 on the surface of the prepreg laminate 2 in sequence, and the edge of the vacuum film 4 is placed on the secondary step of the mold body 1 and is sealed with the mold body 1 by adhesive tape.
[0050] Step 4, negative pressure system: vacuum treatment is performed on the gap between the prepreg laminate 2 and the vacuum film 4, and the vacuum is pumped to 0.2pa.
[0051] Step 5, positive pressure system: cover the mold cov...
Embodiment 2
[0055] Step 1. Treat the mold: Use the mold release agent to wipe the inner surface of the mold body 1 for 2 times, and dry it after each wipe. The interval between each wipe is 3 minutes, and the cumulative thickness of the mold release agent is 0.1mm.
[0056] Step 2, continuous fiber prepreg layering: 8 layers of continuous fiber prepreg are selected for orderly layering on the surface of the mold body 1, and the cumulative thickness is 2 mm to form a prepreg layer 2.
[0057] Step 3, adding auxiliary materials: laying a release cloth and a vacuum film 4 on the surface of the prepreg laminate 2 in sequence, and the edge of the vacuum film 4 is placed on the secondary step of the mold body 1 and is sealed with the mold body 1 by adhesive tape.
[0058] Step 4, negative pressure system: vacuum treatment is performed on the gap between the prepreg laminate 2 and the vacuum film 4, and the vacuum is pumped to 50pa.
[0059] Step 5, positive pressure system: cover the mold cover p...
Embodiment 3
[0063] Step 1. Treat the mold: Use the mold release agent to wipe the inner surface of the mold body 1 for 5 times, and dry after each wipe. The interval between each wipe is 4 minutes, and the cumulative thickness of the mold release agent is 0.1mm.
[0064] Step 2, continuous fiber rapid-curing prepreg layering: 10 layers of continuous fiber prepreg are selected for orderly layering on the surface of the mold body 1, and the cumulative thickness is 2.5 mm to form a prepreg layer 2.
[0065] Step 3, adding auxiliary materials: laying a release cloth and a vacuum film 4 on the surface of the prepreg laminate 2 in sequence, and the edge of the vacuum film 4 is placed on the secondary step of the mold body 1 and is sealed with the mold body 1 by adhesive tape.
[0066] Step 4, negative pressure system: vacuum treatment is performed on the gap between the prepreg laminate 2 and the vacuum film 4, and the vacuum is pumped to 100pa.
[0067] Step 5, positive pressure system: cover ...
PUM
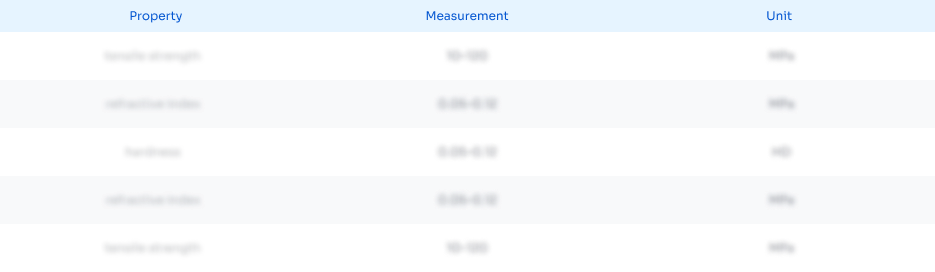
Abstract
Description
Claims
Application Information

- R&D
- Intellectual Property
- Life Sciences
- Materials
- Tech Scout
- Unparalleled Data Quality
- Higher Quality Content
- 60% Fewer Hallucinations
Browse by: Latest US Patents, China's latest patents, Technical Efficacy Thesaurus, Application Domain, Technology Topic, Popular Technical Reports.
© 2025 PatSnap. All rights reserved.Legal|Privacy policy|Modern Slavery Act Transparency Statement|Sitemap|About US| Contact US: help@patsnap.com