Rapid forming method of thermoplastic fiber reinforced composite material board
A fiber-reinforced and composite material technology, which is applied in metal processing and other directions, can solve the problems of low processing efficiency, single drilling function, and cumbersome operation steps of composite material plates, and achieve increased rotation flexibility, simple and convenient clamping work, and improved The effect of work efficiency
- Summary
- Abstract
- Description
- Claims
- Application Information
AI Technical Summary
Problems solved by technology
Method used
Image
Examples
Embodiment Construction
[0016] Combine below Figure 1-2 The present invention will be described in detail.
[0017] refer to Figure 1-2 , according to an embodiment of the present invention, a rapid prototyping method of a thermoplastic fiber-reinforced composite material plate, including a base plate 100 and vertical stands 103 symmetrically fixed on the left and right sides of the base plate 100, and the left and right sides A rotating ring 109 is installed between the vertical frames 103, and the bottom end surface of the rotating ring 109 is fixed with a manufacturing frame 111, and the left and right symmetrical air pressure chambers 115 are arranged in the manufacturing frame 111, and the sliding fit in the air pressure chamber 115 A compression plate 112 is installed, and the opposite end faces of the compression plates 112 on the left and right sides are fixed with a distance-adjusting frame 122, and the distance-adjusting frame 112 protrudes from the outer end of the manufacturing frame 1...
PUM
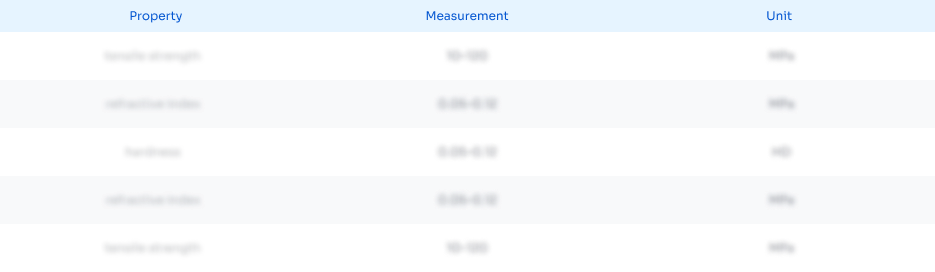
Abstract
Description
Claims
Application Information

- R&D Engineer
- R&D Manager
- IP Professional
- Industry Leading Data Capabilities
- Powerful AI technology
- Patent DNA Extraction
Browse by: Latest US Patents, China's latest patents, Technical Efficacy Thesaurus, Application Domain, Technology Topic, Popular Technical Reports.
© 2024 PatSnap. All rights reserved.Legal|Privacy policy|Modern Slavery Act Transparency Statement|Sitemap|About US| Contact US: help@patsnap.com