A kind of preparation method of zinc manganate/silver composite material
A composite material, zinc manganate technology, applied in the direction of structural parts, electrical components, battery electrodes, etc., can solve the problems of poor charge and discharge cycle ability, achieve improved conductivity, simple co-precipitation method, improve initial Coulombic efficiency and cycle The effect of stability
- Summary
- Abstract
- Description
- Claims
- Application Information
AI Technical Summary
Problems solved by technology
Method used
Image
Examples
Embodiment 1
[0024] 1) Dissolve the raw materials zinc nitrate, manganese nitrate and silver nitrate in deionized water, wherein the amount of zinc nitrate is 1.0g, the amount of manganese nitrate is 2.0g, the amount of silver nitrate is 0.1g, and the amount of deionized water is 50mL , the solution was stirred for 10 minutes to form a uniform solution;
[0025] 2) Dissolve 10 g of oxalic acid as a raw material in 50 mL of absolute ethanol, and stir the solution for 10 minutes to form a uniform solution;
[0026] 3) Add the solution described in step 1) dropwise to the solution described in step 2), and keep stirring;
[0027] 4) Centrifuge the above solution to separate the precipitate, wash with ethanol and deionized water respectively, dry the precipitate at 60°C for 360min, then put the dried precipitate into a tube furnace and calcinate at 400°C for 120min to obtain Zinc manganate / silver composite.
Embodiment 2
[0029] 1) Dissolve the raw materials zinc nitrate, manganese nitrate and silver nitrate in deionized water, wherein the amount of zinc nitrate is 2.0g, the amount of manganese nitrate is 4.0g, the amount of silver nitrate is 0.2g, and the amount of deionized water is 60mL , the solution was stirred for 15 minutes to form a uniform solution;
[0030] 2) Dissolve 12g of oxalic acid as a raw material in 60mL of absolute ethanol, and stir the solution for 15 minutes to form a uniform solution;
[0031] 3) Add the solution described in step 1) dropwise to the solution described in step 2), and keep stirring;
[0032] 4) Centrifuge the above solution to separate the precipitate, wash with ethanol and deionized water respectively, dry the precipitate at 65°C for 380min, then put the dried precipitate into a tube furnace and calcinate at 450°C for 150min to obtain Zinc manganate / silver composite.
Embodiment 3
[0034] 1) Dissolve the raw materials zinc nitrate, manganese nitrate and silver nitrate in deionized water, wherein the amount of zinc nitrate is 3.0g, the amount of manganese nitrate is 6.0g, the amount of silver nitrate is 0.3g, and the amount of deionized water is 70mL , the solution was stirred for 18 minutes to form a uniform solution;
[0035] 2) Dissolve 15g of oxalic acid as a raw material in 70mL of absolute ethanol, and stir the solution for 18 minutes to form a uniform solution;
[0036] 3) Add the solution described in step 1) dropwise to the solution described in step 2), and keep stirring;
[0037] 4) Centrifuge the above solution to separate the precipitate, wash with ethanol and deionized water respectively, dry the precipitate at 68°C for 400min, then put the dried precipitate into a tube furnace and calcinate at 480°C for 180min to obtain Zinc manganate / silver composite.
PUM
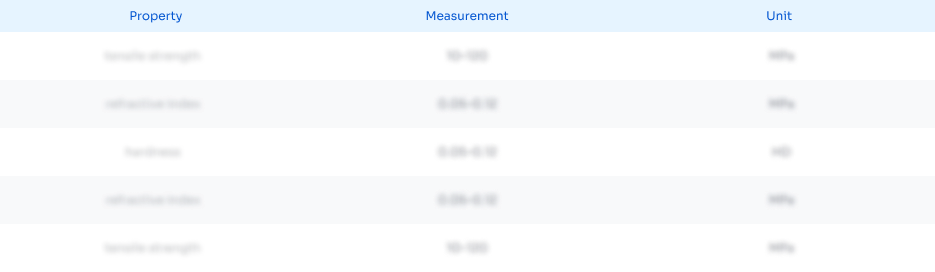
Abstract
Description
Claims
Application Information

- R&D
- Intellectual Property
- Life Sciences
- Materials
- Tech Scout
- Unparalleled Data Quality
- Higher Quality Content
- 60% Fewer Hallucinations
Browse by: Latest US Patents, China's latest patents, Technical Efficacy Thesaurus, Application Domain, Technology Topic, Popular Technical Reports.
© 2025 PatSnap. All rights reserved.Legal|Privacy policy|Modern Slavery Act Transparency Statement|Sitemap|About US| Contact US: help@patsnap.com